Holzscheiben herstellen
Zur Herstellung kreisrunder Holzobjekte gibt es eine ganze Anzahl unterschiedlicher Verfahren. Die Drechselbank liegt nahe, mit der Bandsäge kann man annähernd Kreise schneiden und wieder andere verwenden eine Schleifscheibe.
Alle Verfahren haben Vor- und Nachteile, angefangen von einer erheblichen Menge Schleifstaub, Nacharbeit oder einfach nur der Tatsache, dass nicht jeder die benötigte Maschine besitzt. Natürlich spielen auch die Vorlieben des Bearbeiters eine wichtige Rolle.
So geht es mir - Maschine der Wahl ist die Oberfräse, danach kommt die Bandsäge. Beide zusammen helfen, auch recht dicke runde Werkstücke anzufertigen. Die Vorgehensweise wird hier erklärt.
Als Ausgangsmaterial kommt Buche mit einer Stärke zwischen 45 und 50 mm zu Einsatz.
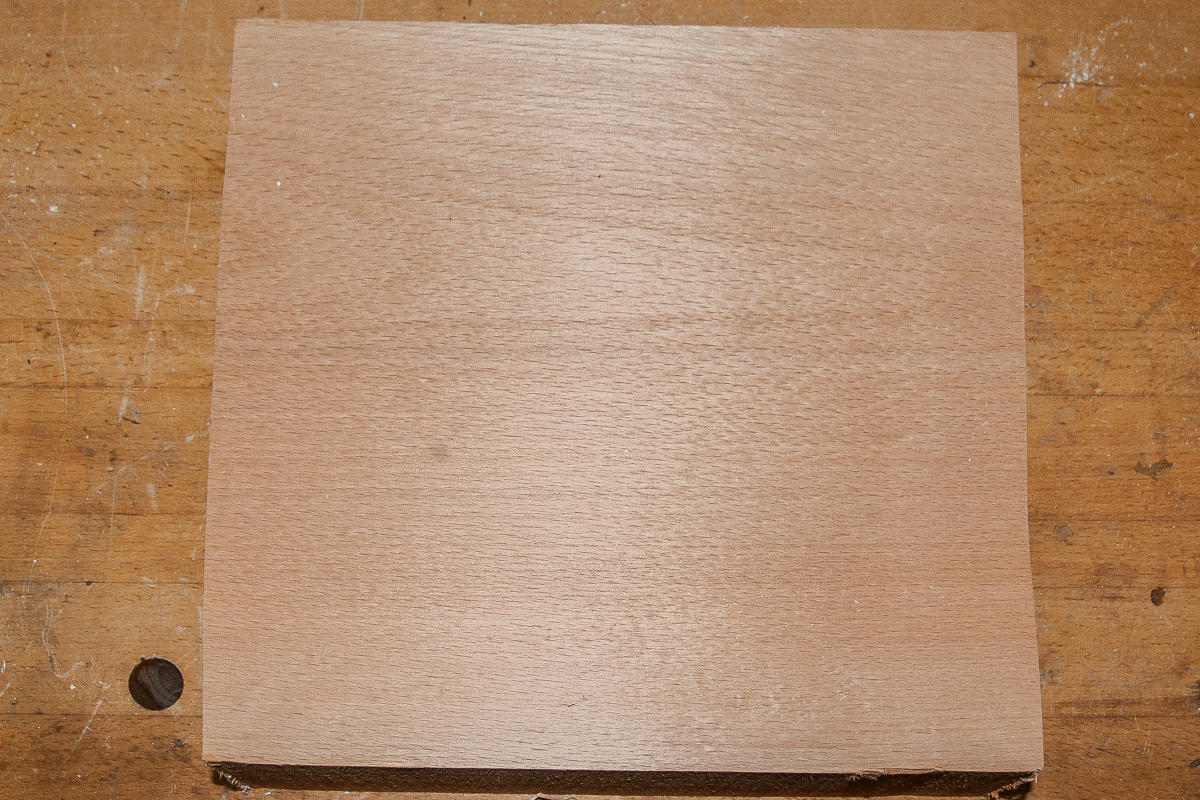
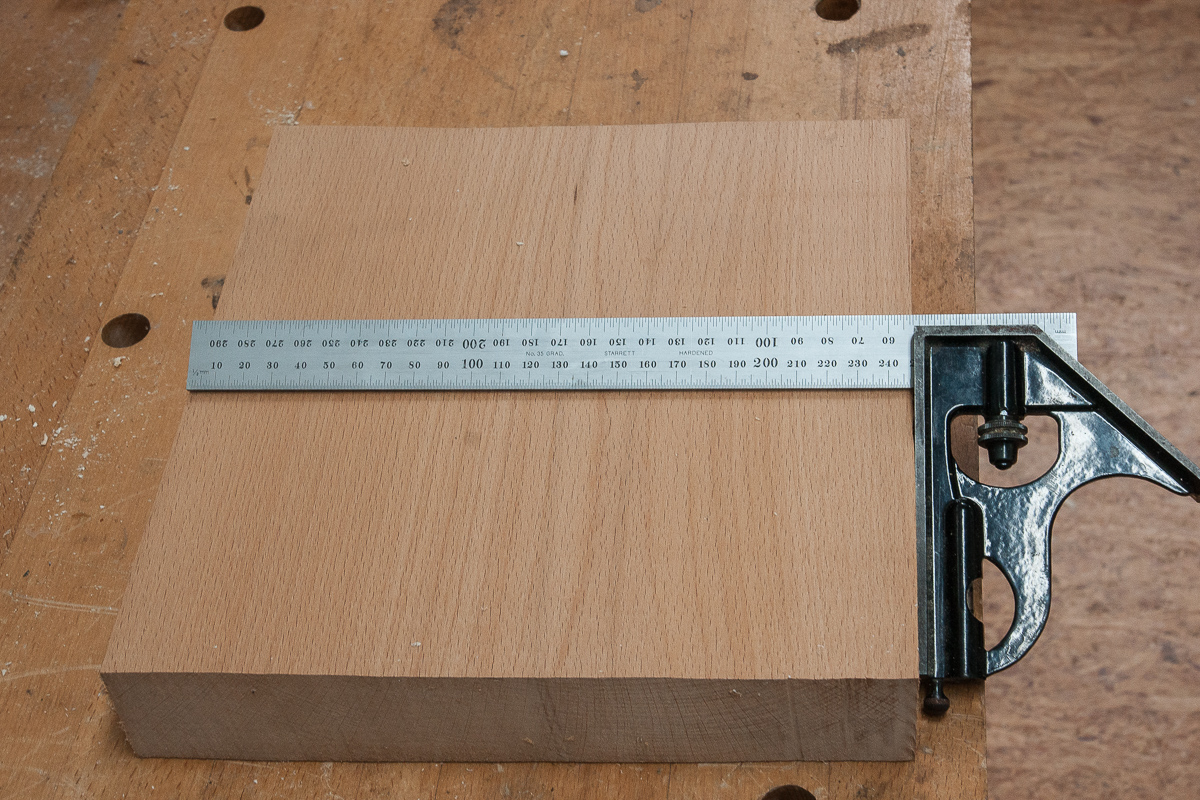
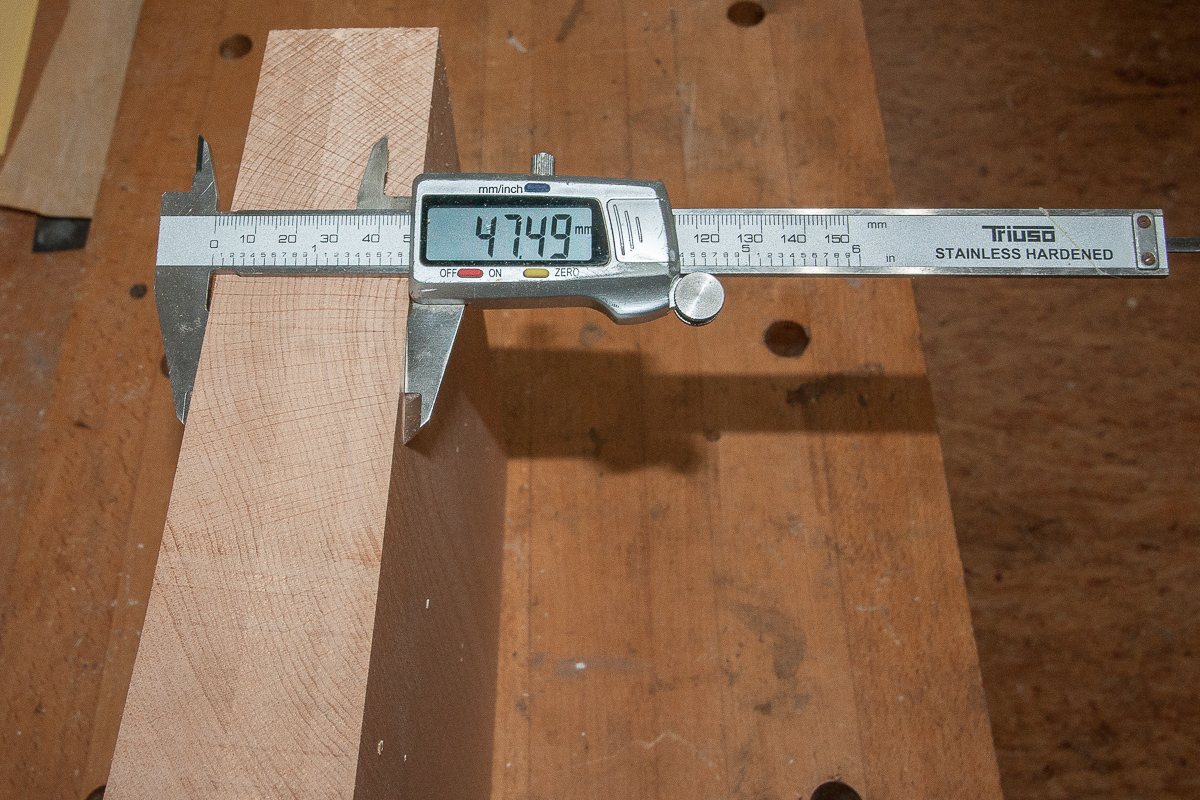
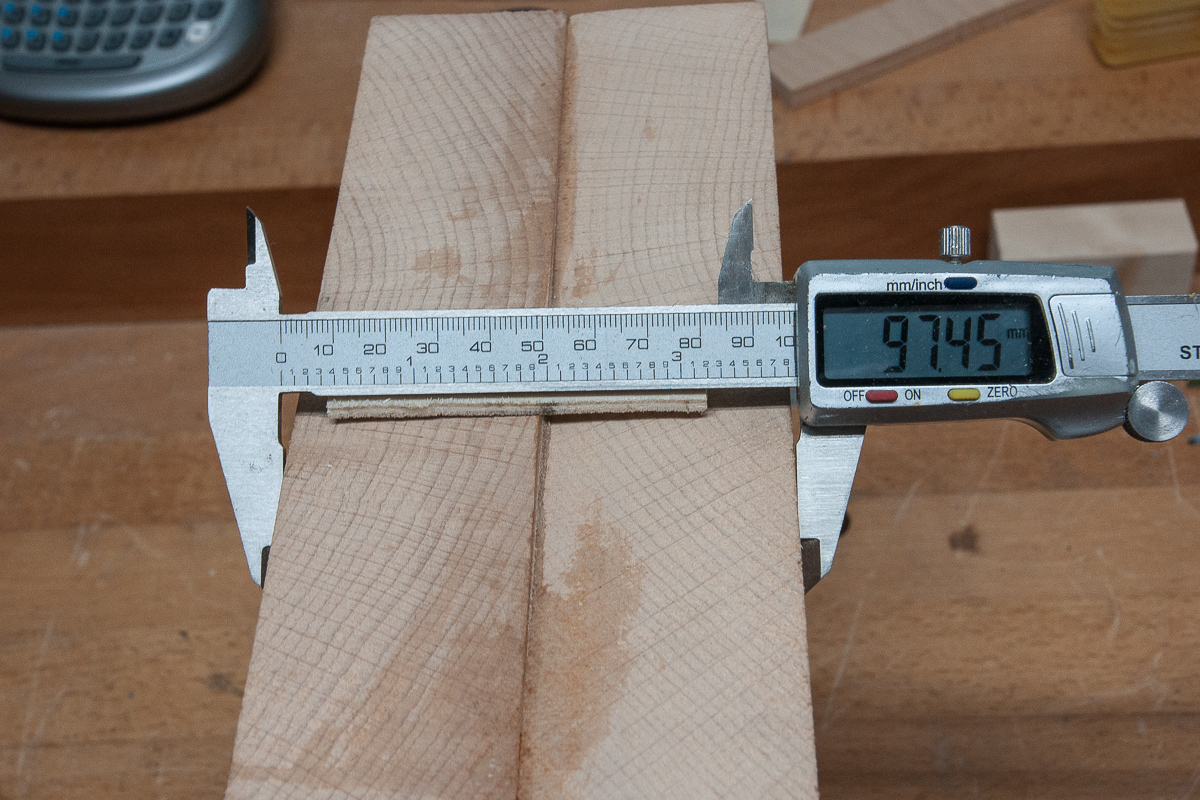
Die Rohlinge sind so, wie sie vom Brett abgeschnitten wurden, also nicht unbedingt genau quadratisch.
Jetzt wird der ungefähre Mittelpunkt bestimmt:
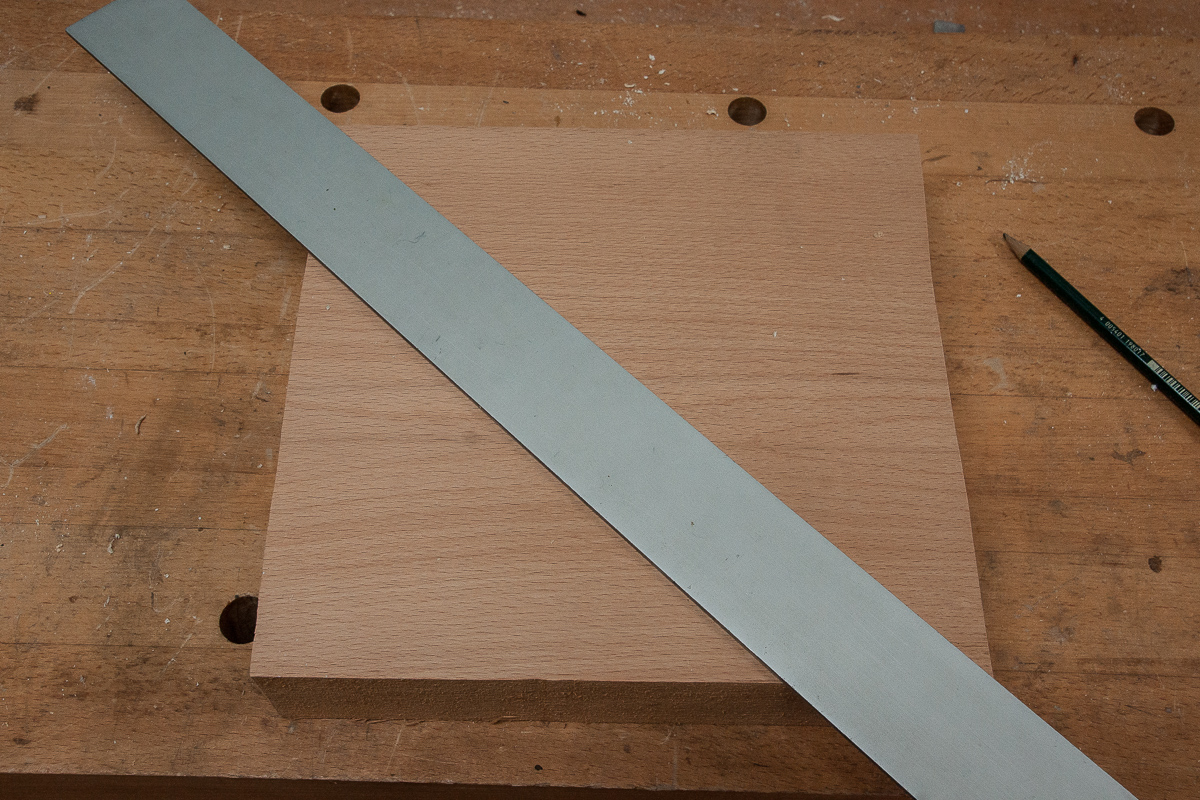
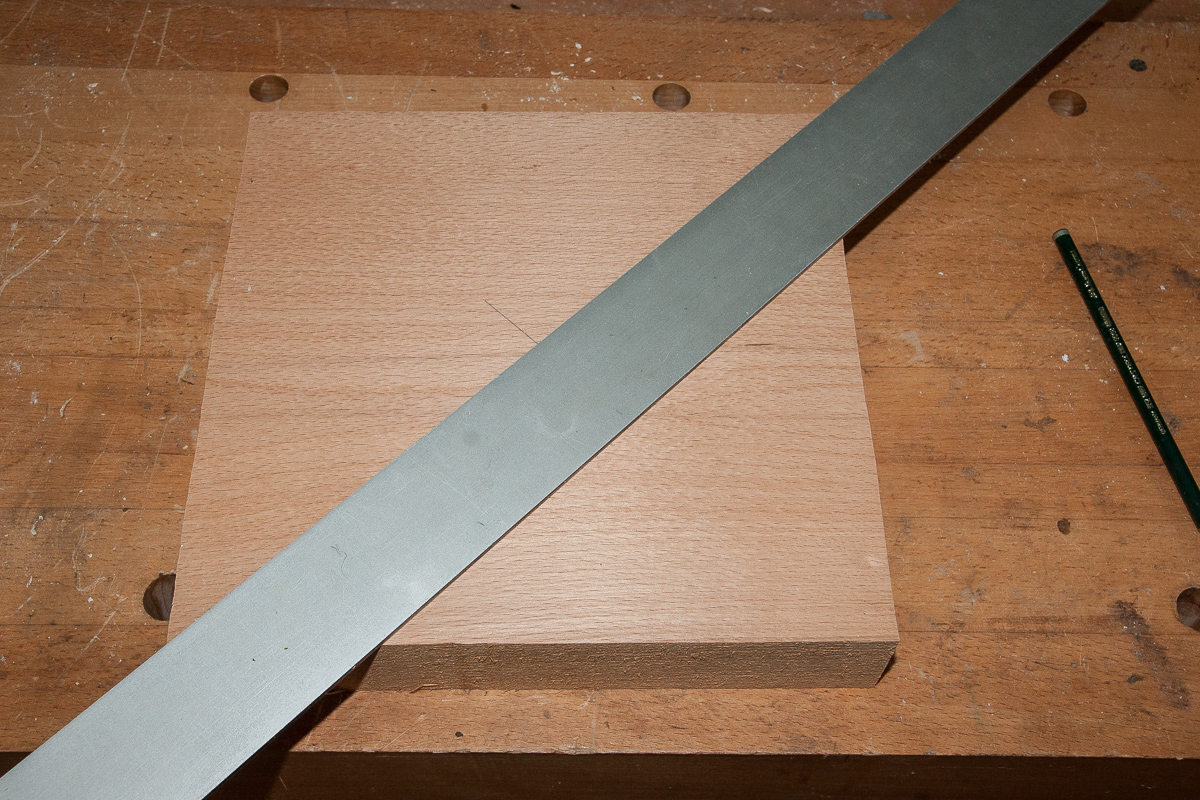
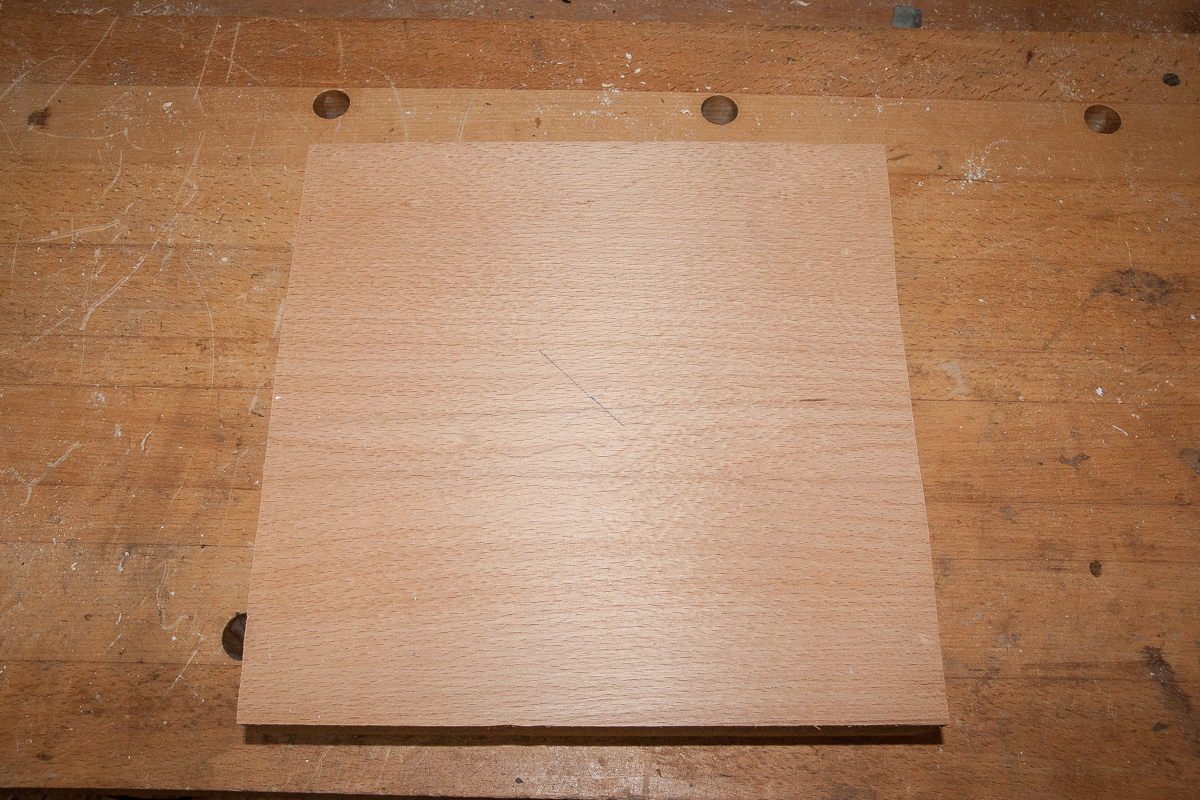
Das Anschneiden der Kreisform erfolgt mit der handgeführten Oberfräse auf der Hobelbank. Dazu muss das Werkstück sicher fixiert werden. Zum Einsatz kommt ein Bankhaken und drei so genannte "Wonder Dogs", also verstellbare Spannelemente, alle mit 3/4 Zoll Schaft. Diese runden Bankspannelemente haben den entscheidenden Vorteil, dass sie sich bei nicht rechtwinkliger Werkstückkante drehen und damit anpassen können.

Zuerst muss der Werkstück-Mittelpunkt angebohrt werden.
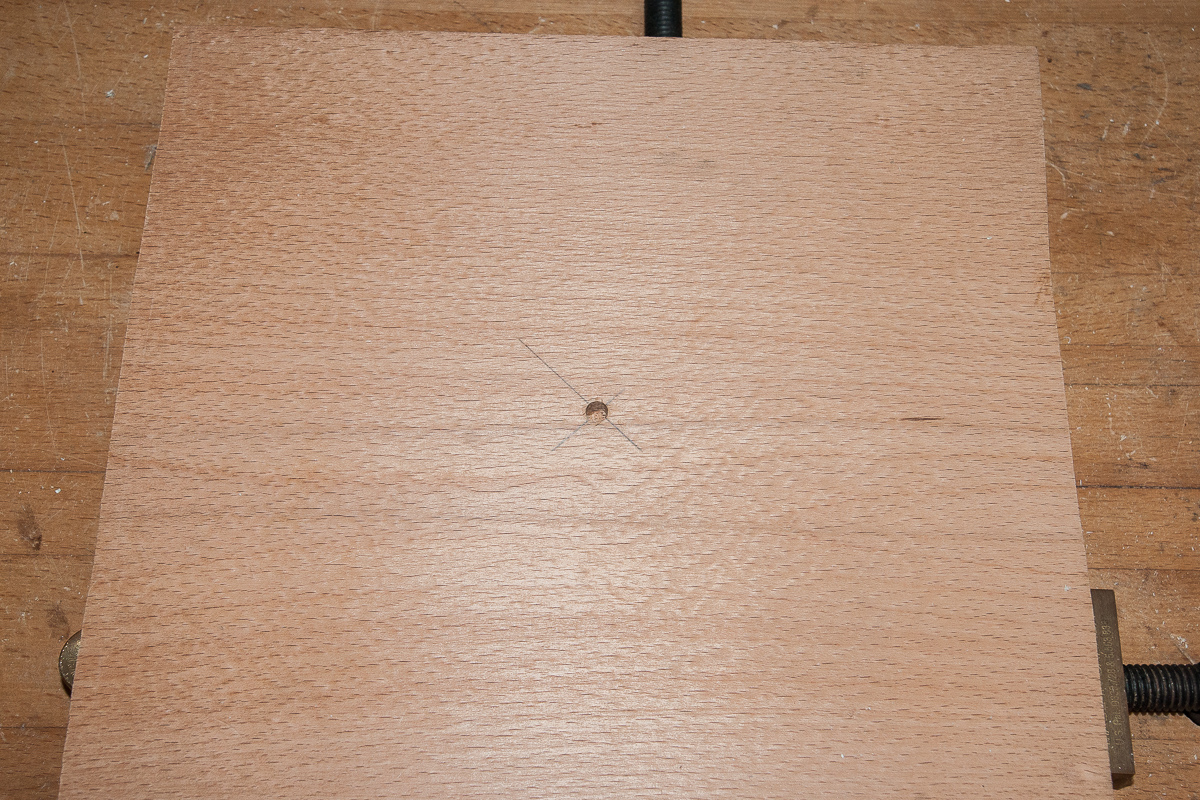
Diese Bohrung führt den Fräszirkel, kann also je nach eingesetztem Werkzeug in unterschiedlicher Tiefe/Durchmesser nötig sein.
Wer keine Bohrung im Werkstück möchte klebt mit doppelseitigem Klebeband 6mm (oder auch stärker) Sperrholz auf, in dem sich die Zentrumsbohrung befindet. Das Sperrholz muss aber mindestens so gross sein, dass die Maschine in keiner Richtung abkippt.
Als Fräszirkel wird die Combination Router Base (CRB) von Trend verwendet. Mit ihr kann man Kreise mit einem Duchmesser von 38 - 448 mm herstellen.
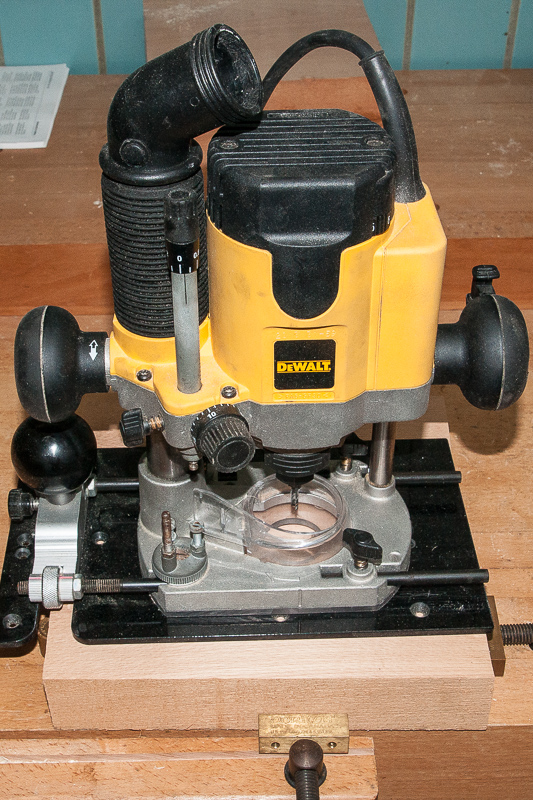
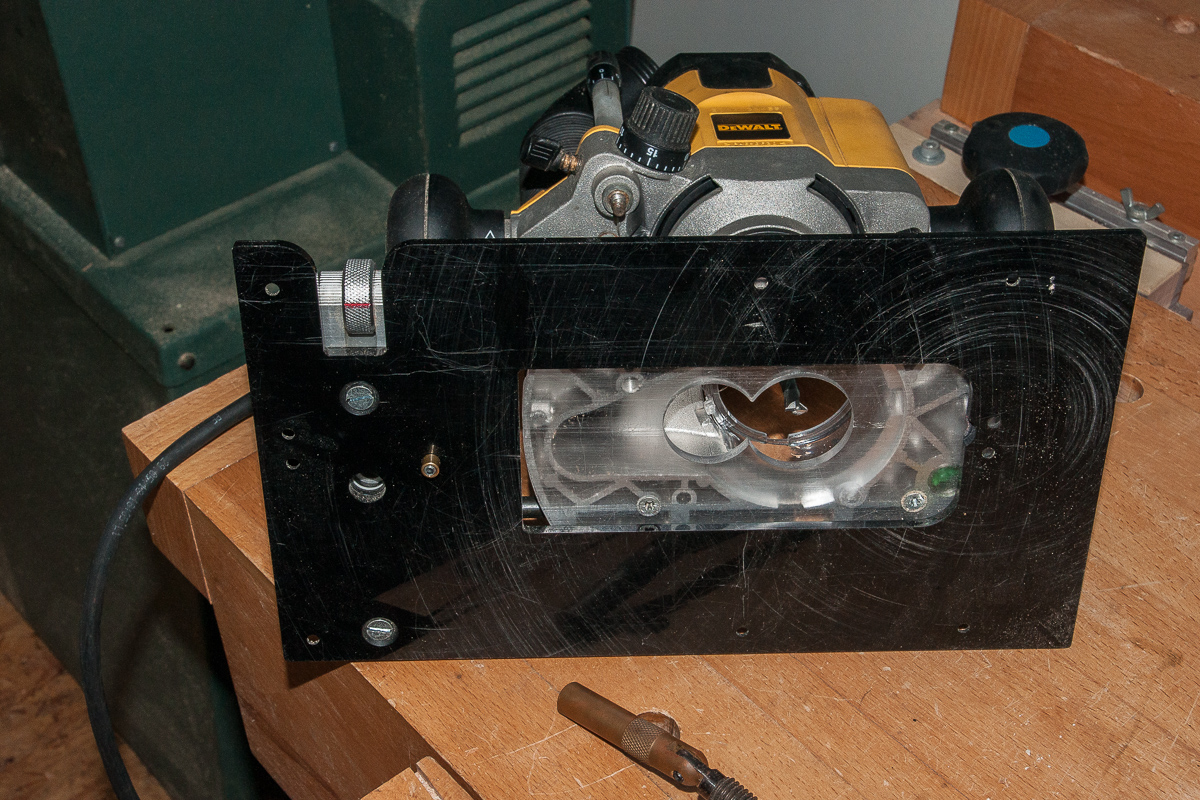
Der kleine goldfarbene Pin in der Mitte links wird in die Zentrumsbohrung eingesetzt, führt die Maschine gut. Die recht grosse Bodenplatte stabilisiert zusätzlich.
Oben links ein Stellrad, mit dem man den Duchmesser feinjustieren kann, falls das erforderlich sein sollte.
Man braucht nicht unbedingt so eine Vorrichtung zum Kreise schneiden, eine einfache Spitze am Ende einer Führungsstange des Parallelanschlags tut es auch; andere Fräszirkel ebenso.
Nach Anbringen von Fräse und Zirkel auf dem Werkstück sollte man nach allen vier Richtungen prüfen, wo sich denn die kürzeste Distanz zwischen Führungsbohrung und Kante findet. Das ist dann der grösstmögliche Radius, den man schneiden kann. Dabei sollte der Fräser auch dort immer noch ein kleines Stück ins Holz schneiden.
Gefräst wird mit einem 8 mm starken Vollhartmetallfräser mit aufwärts schneidenden Spiralen. Maximale Frästiefe ist 35 mm, also nicht genug um die gezeigten Werkstücke ganz durchzufräsen. Die Drehzahl der Fräse wird auf 13 - 15.000 U/min reduziert. Das verhindert Brandspuren am dafür recht anfälligen Buchenholz. Die Tiefe pro Fräsdurchgang beträgt ca. 7,5 mm, so dass 4 Umläufe nötig sind.
Wie das weitergeht steht dann unten.
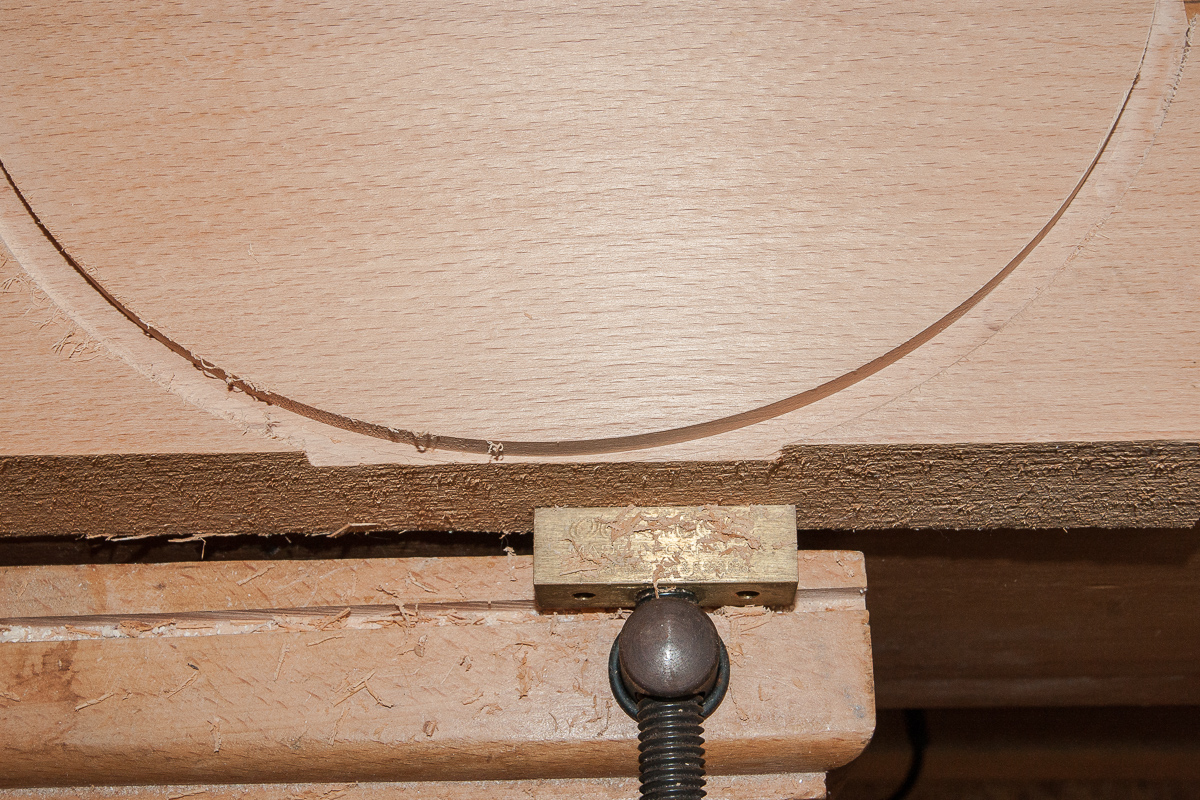
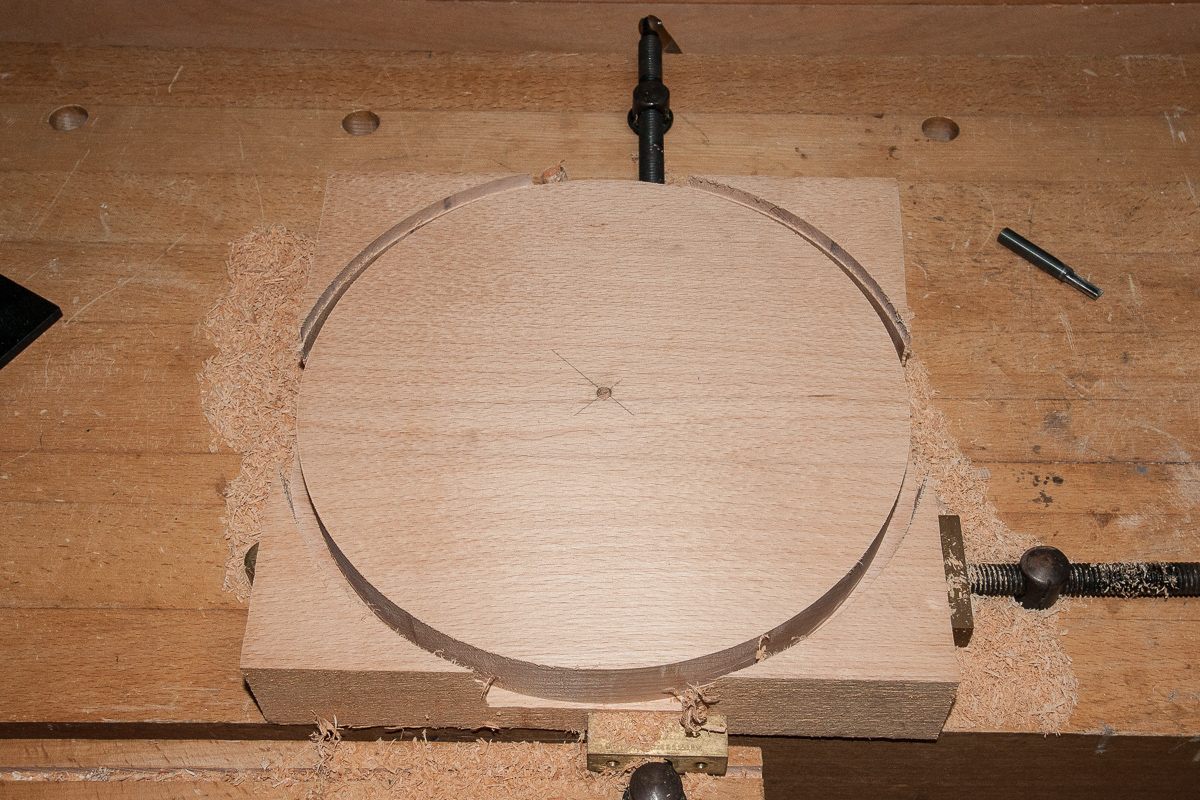
Die Fräsung im Bild hat eine Tiefe von rund 30 mm.
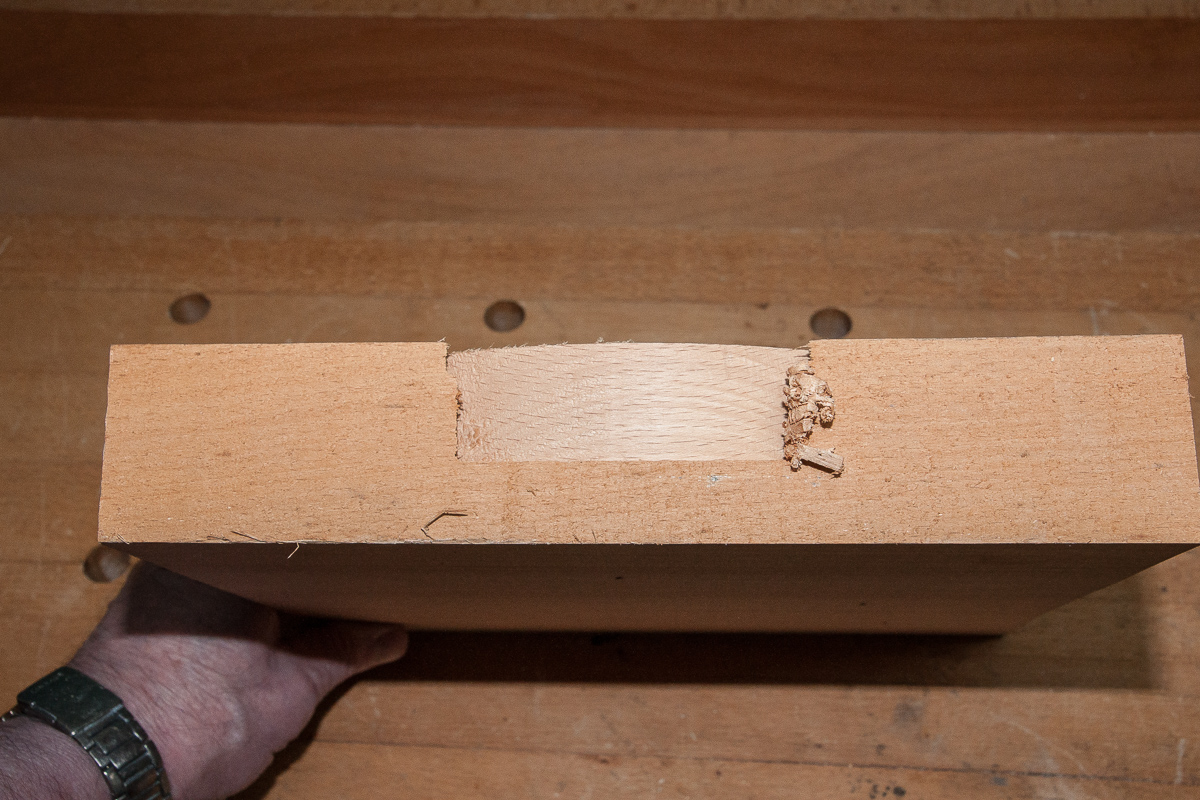
Den Rest muss die Bandsäge erledigen. Zwar hätte ich einen Fräser mit 50,8 mm Länge, aber keinen stirnschneidenden.
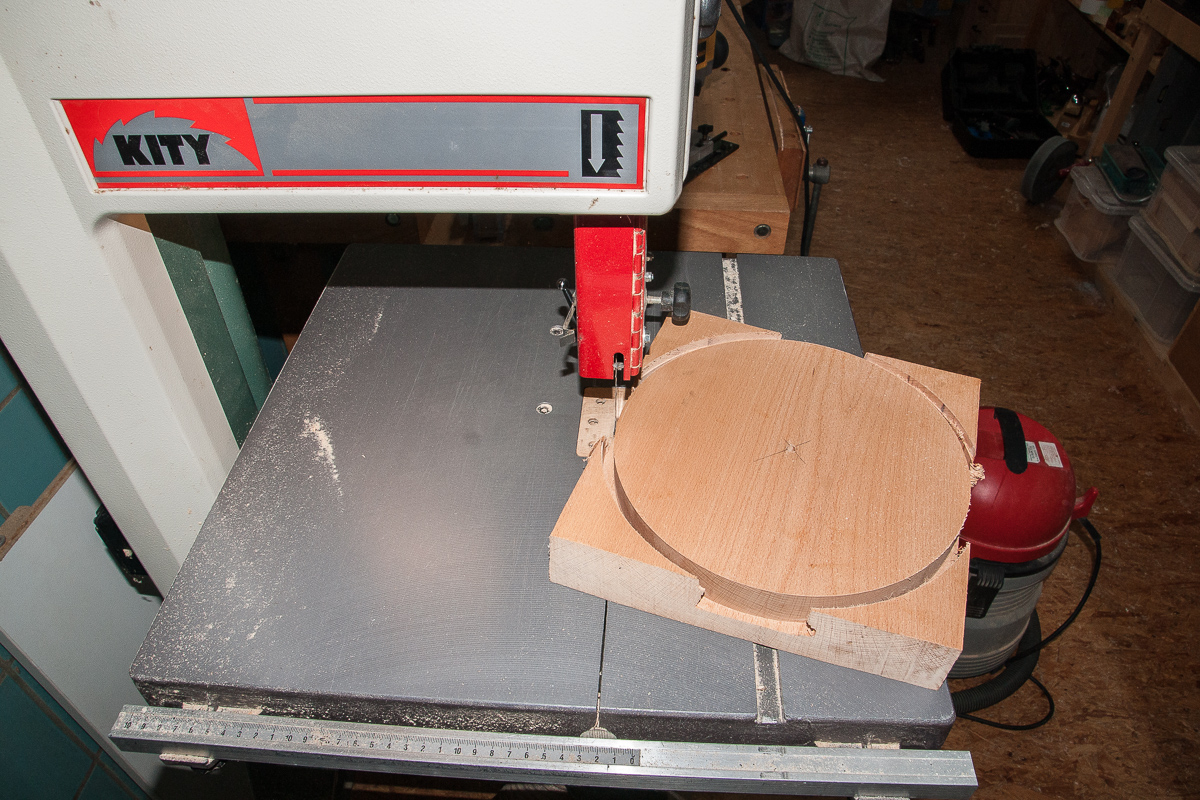
Auf der Bandsäge läuft ein 25 mm breites Band. Damit kann man dem Bogen natürlich nicht folgen, schneidet in mehreren Schritten tangential. Möglichst nahe am vorgegebenen Kreis bleiben, aber nicht aus Versehen hineinschneiden.
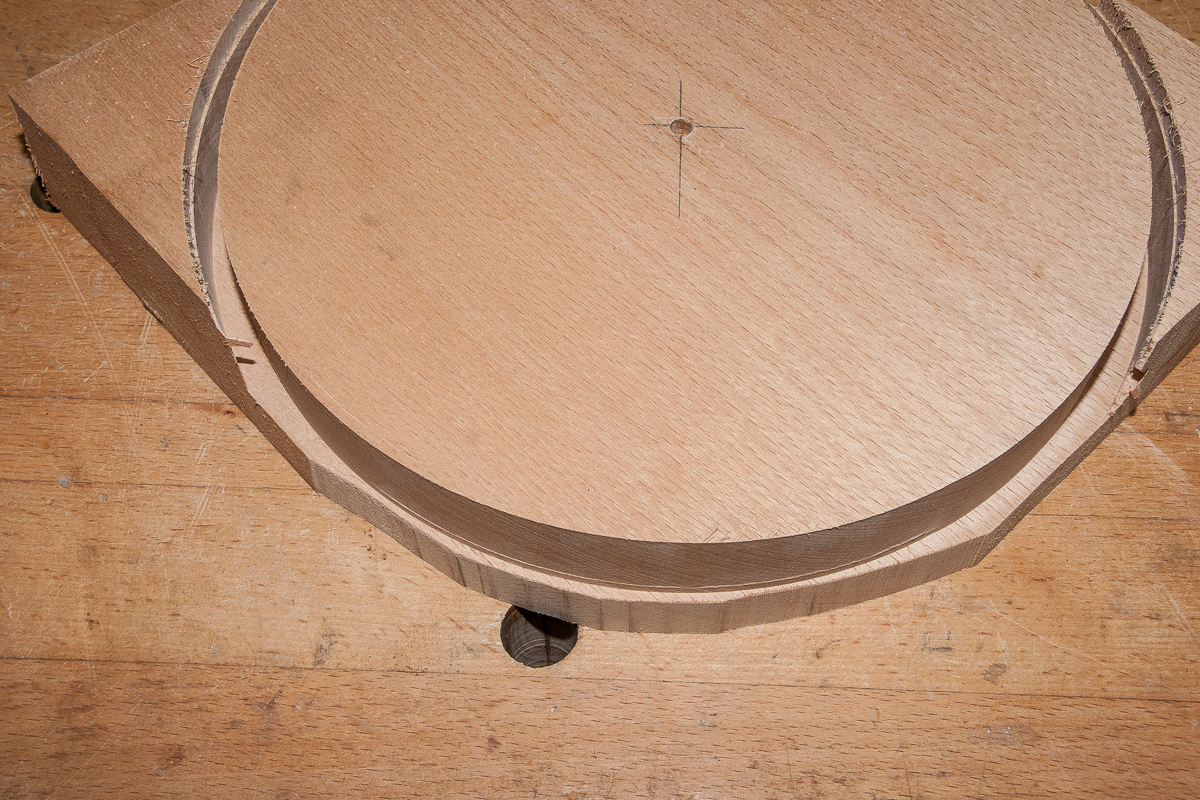
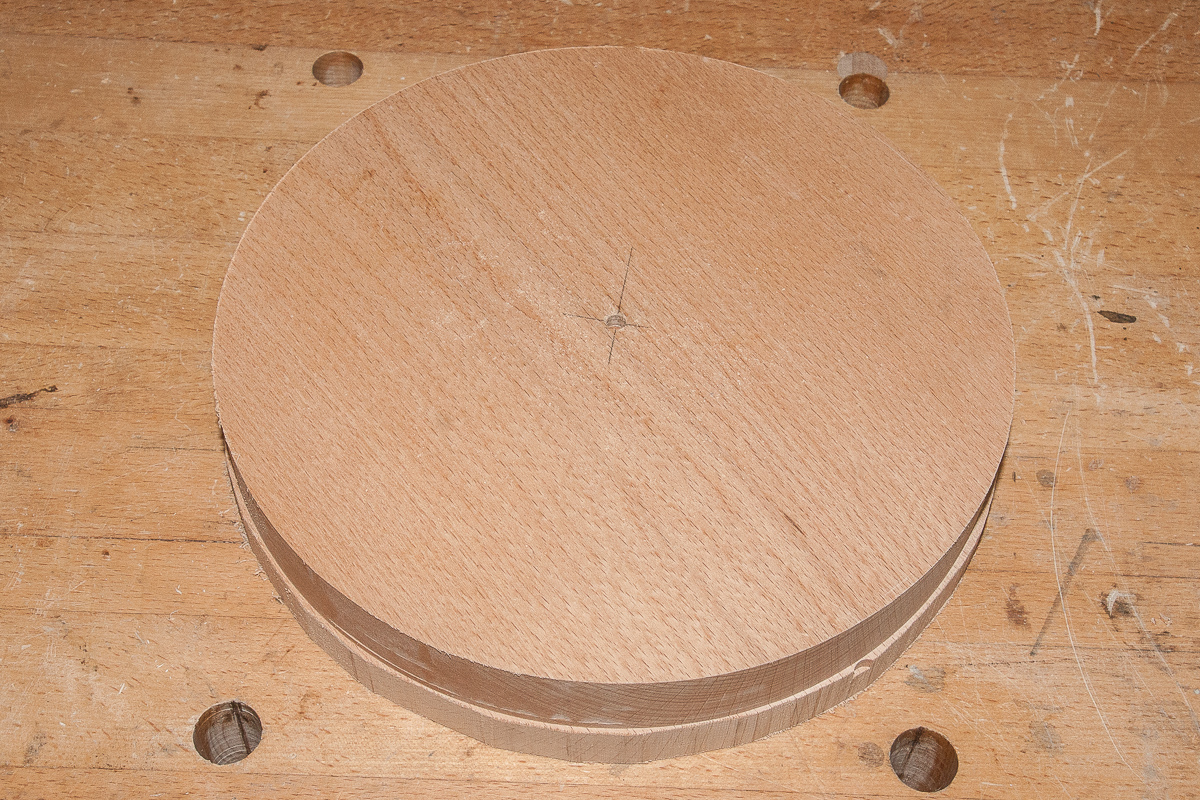
Wie geht es jetzt weiter?
Die Oberfräse im Frästisch kommt zum Einsatz. Mit einem langen Bündigfräser! Dessen Führungskugellager läuft auf dem sauber ausgefrästen Kreis entlang, der Fräser entfernt die nach dem Sägen noch verbliebenen Überstände im unteren Bereich.
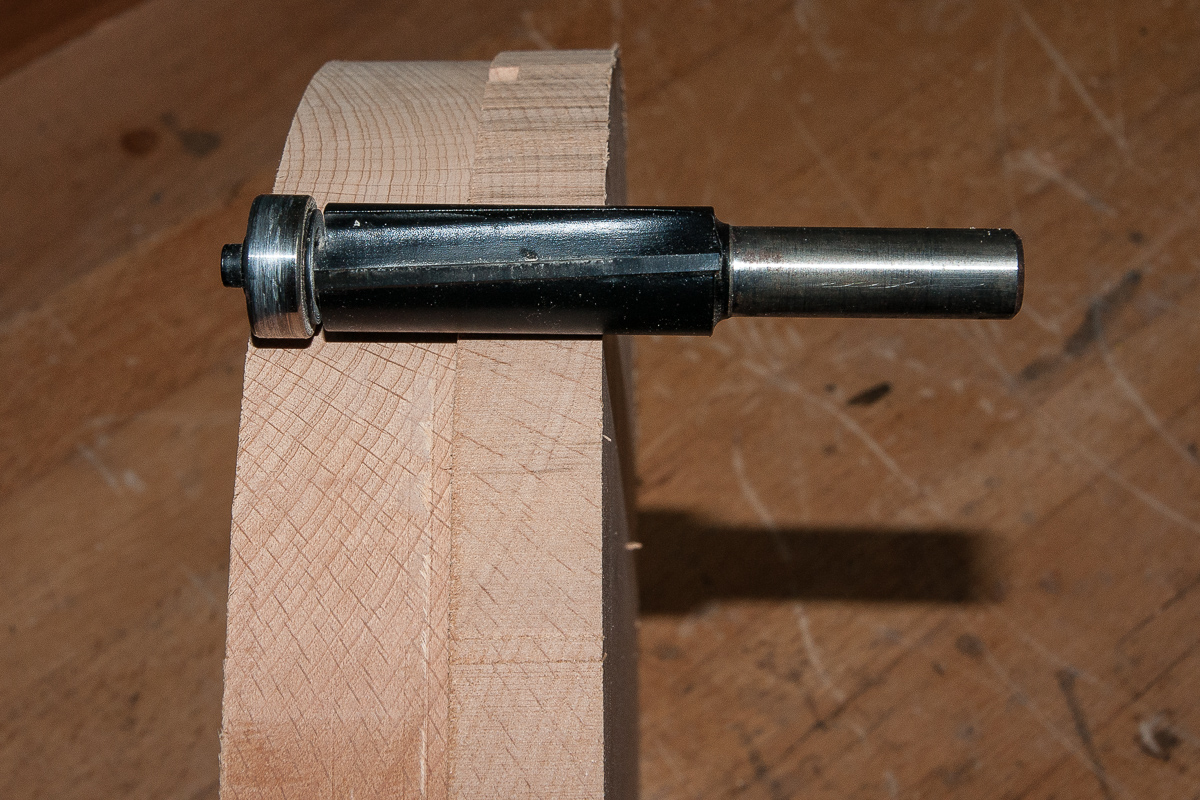
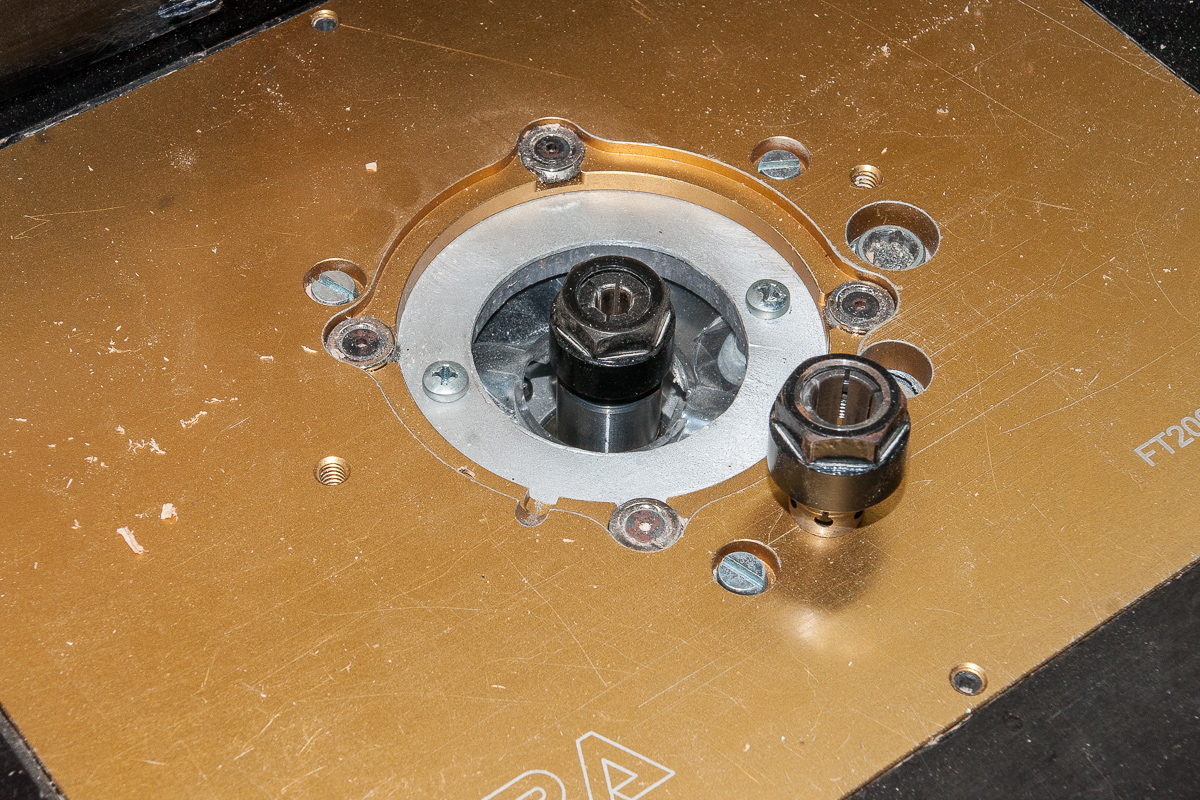
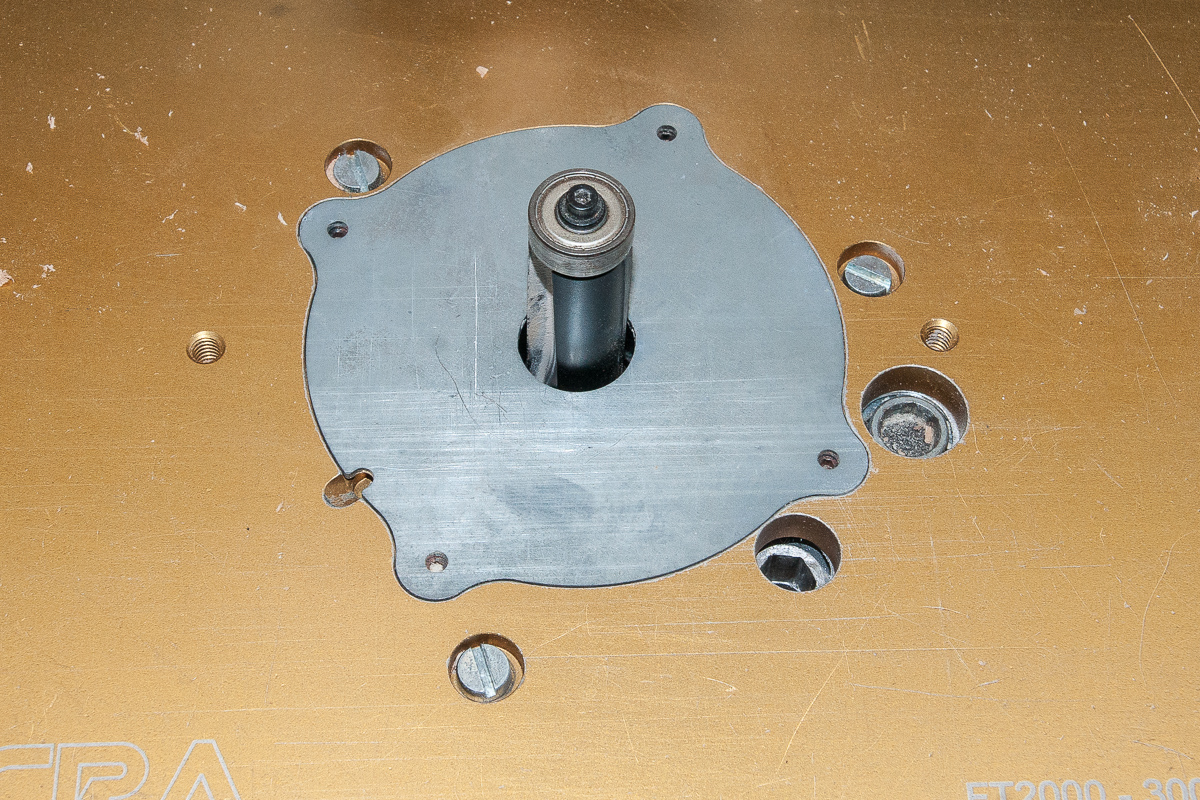
Der Fräser hat 19 (19,05) mm Durchmesser, die Öffnung im Reduzierring beträgt 22,3 mm. Mehr muss nicht sein, ist sogar nachteilig. Die enge Paarung reduziert die Späne unter dem Tisch deutlich. Der schon saubere Teil des Werkstücks befindet sich oben.
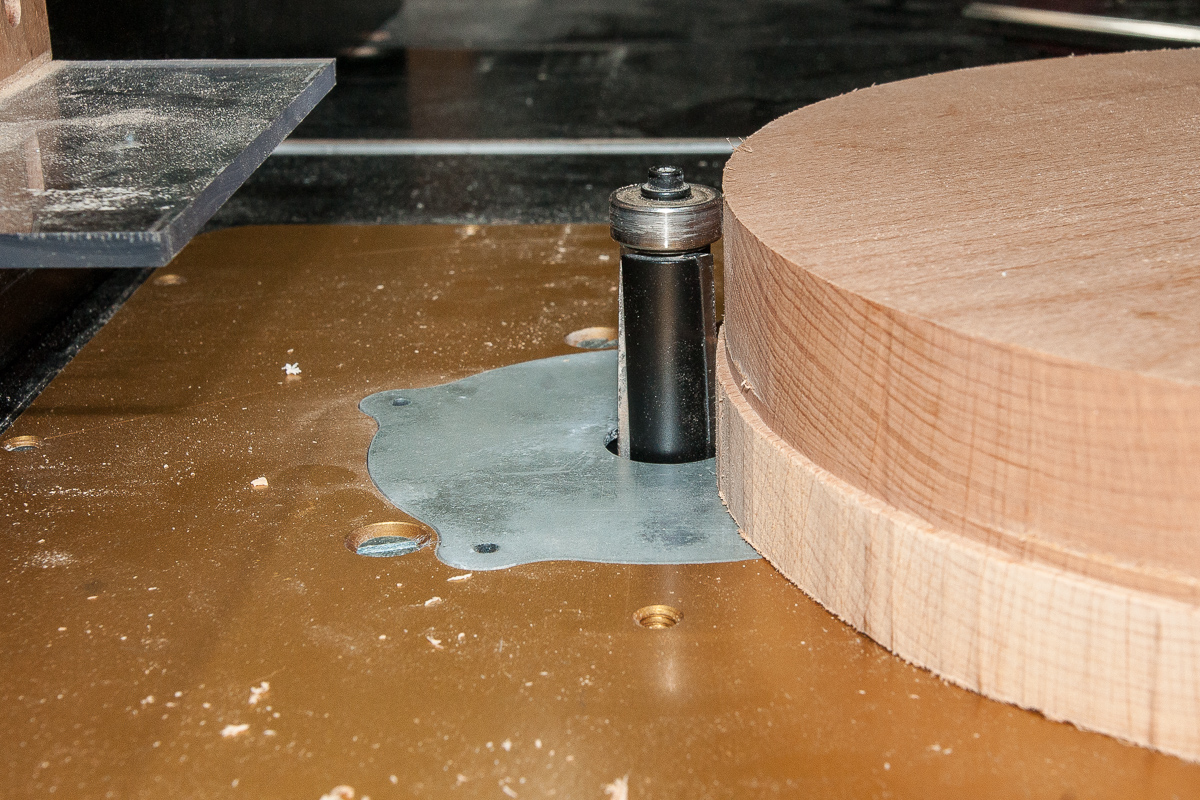
So wird man allerdings nicht arbeiten - es ist einfach gefährlich, einen offen laufenden Fräser auf dem Tisch zu haben. Das Bild dient nur zur Verdeutlichung der Frässituation!
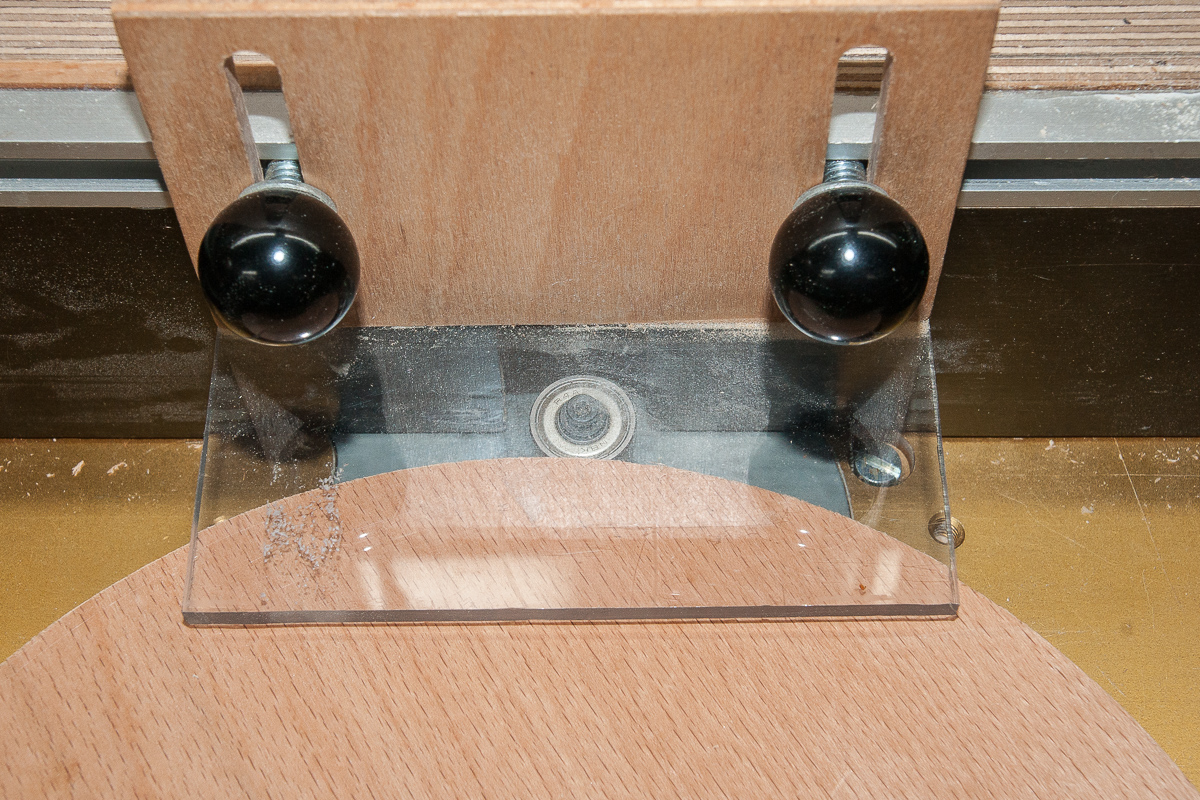
Auch dieses Bild dient nur als Beispiel, gearbeitet wird so nicht. Der Fräser steht deutlich zu weit vor dem Fräsanschlag.
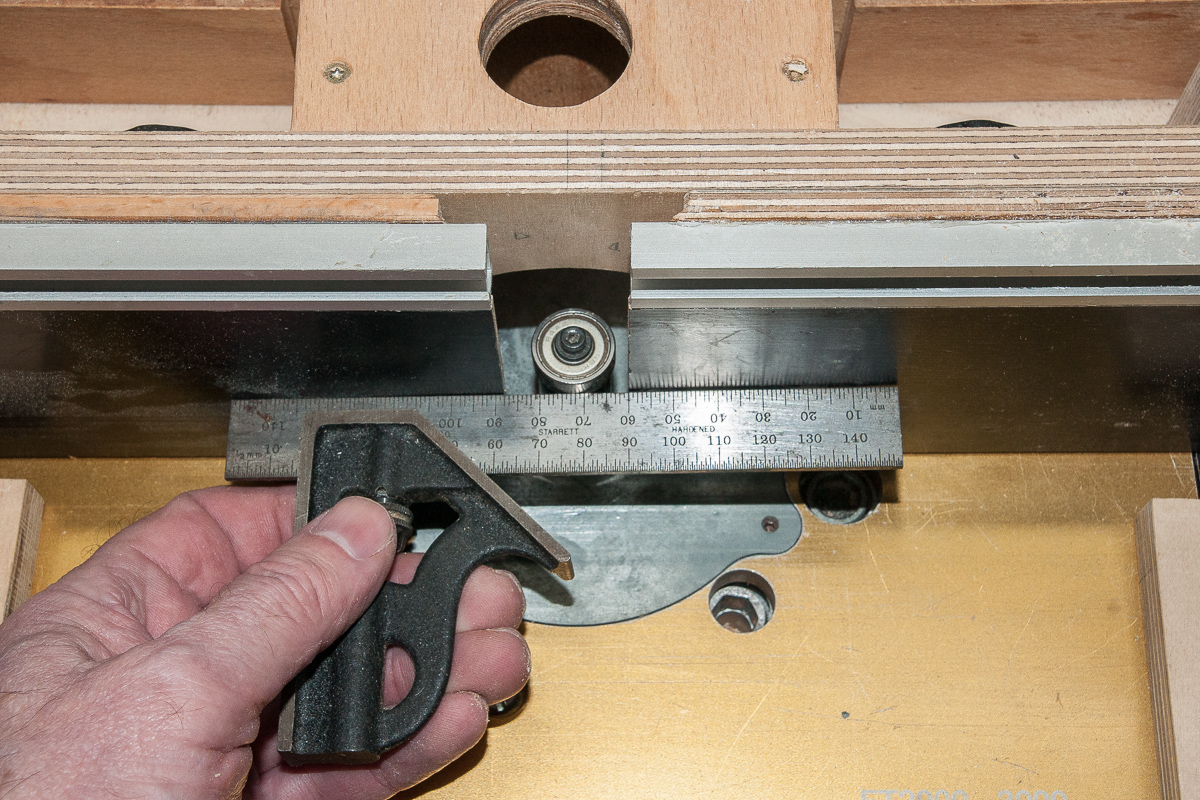
Auch auf dem Tisch wird die Fräse auf die schon einmal genannten 13 - 15.000 U/min eingestellt, um keine Brandspuren zu erzeugen.
Zusätzlich werden die Anschlagbacken möglichst eng an den Fräser herangestellt. So kann sich das Werkstück nicht verhaken, die Spanabnahme bleibt klein und damit auch die Rückschlagneigung. Das Werkstück wird stets gegen den Uhrzeigersinn gedreht.
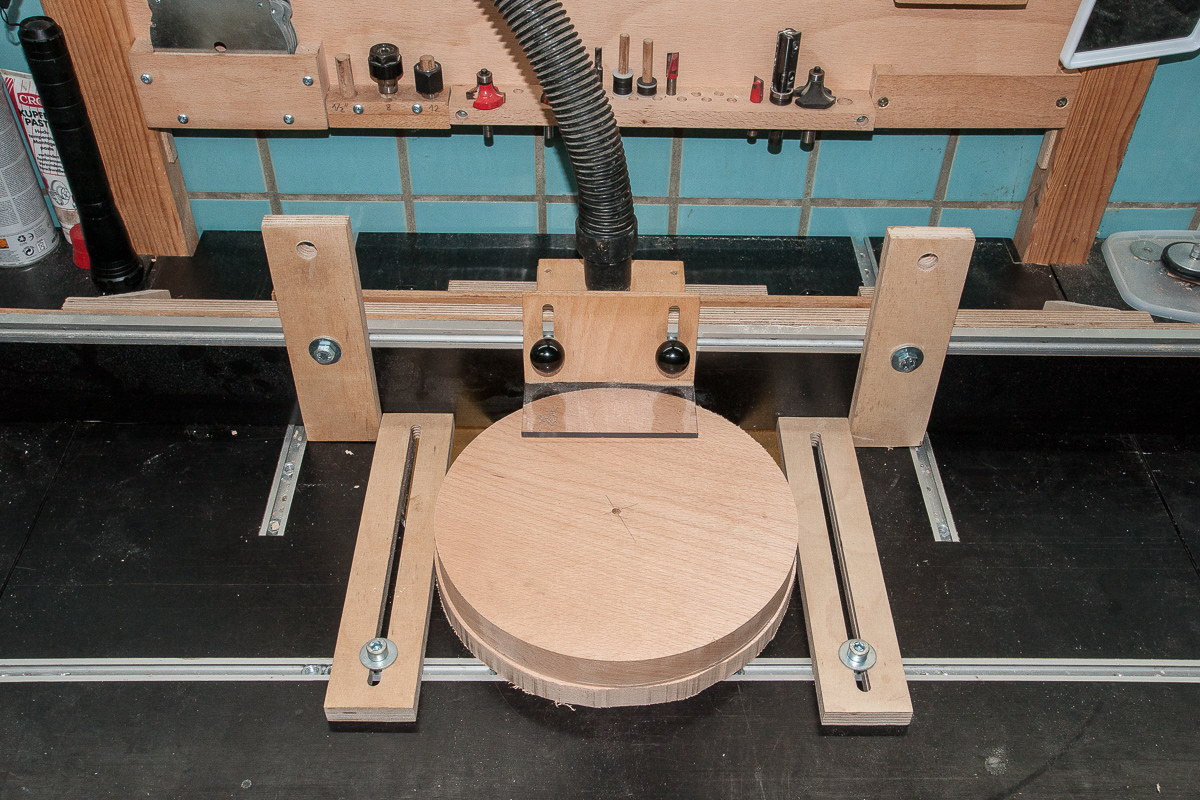
Die Hölzer dienen zusätzlich dem Rückschlagsschutz, die Fräserabdeckung verhindert sicher, dass die Finger in die Nähe der Schneiden kommen können.
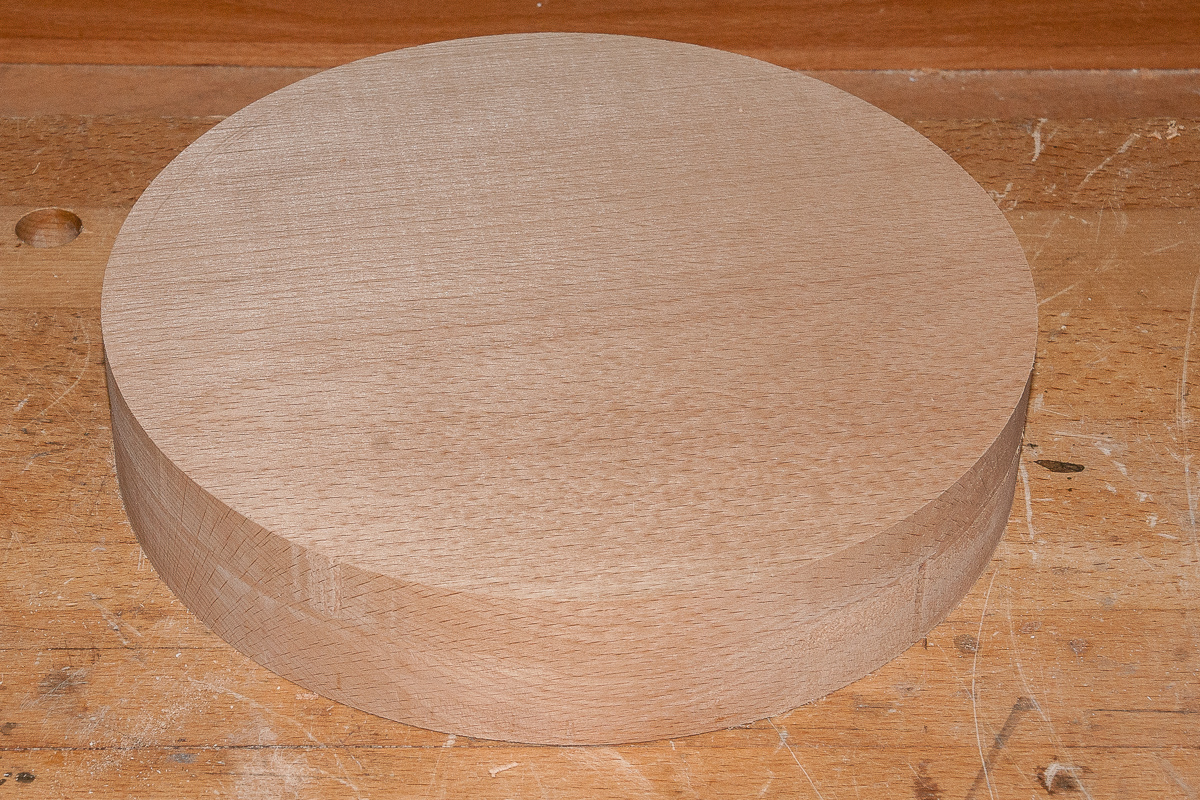
Und wie geht das nun mit dem dickeren Werkstück?
Im Prinzip sehr ähnlich, mit kleineren Anpassungen.
Da es keinen Konflikt zwischen dem Spiral-Nutfräser und den Wonder Dogs gibt, wird mittels Zirkel bis zur vollen möglichen Tiefe gefräst, die bei 35 mm liegt. Wegen der grösseren Frästiefe werden 5 Umläufe gemacht. Danach geht es wieder an die Bandsäge zum Abtrennen des Abfalls.
Die eigentliche Änderung beim Herstellen betrifft das Endfräsen auf dem Frästisch. Mit 35 mm bearbeiteter Höhe und noch einmal 50,8 mm Bündigfräserhöhe sind die gut 97 mm nicht bearbeitbar. Da muss ein Zwischenschritt her!
Im Frästisch kommt zunächst ein 47,6 mm langer Bündigfräser mit am Schaft montierten Kugellager zum Einsatz. Das Werkstück wird dieses Mal mit dem bearbeiteten Teil nach unten auf die Tischplatte gelegt.
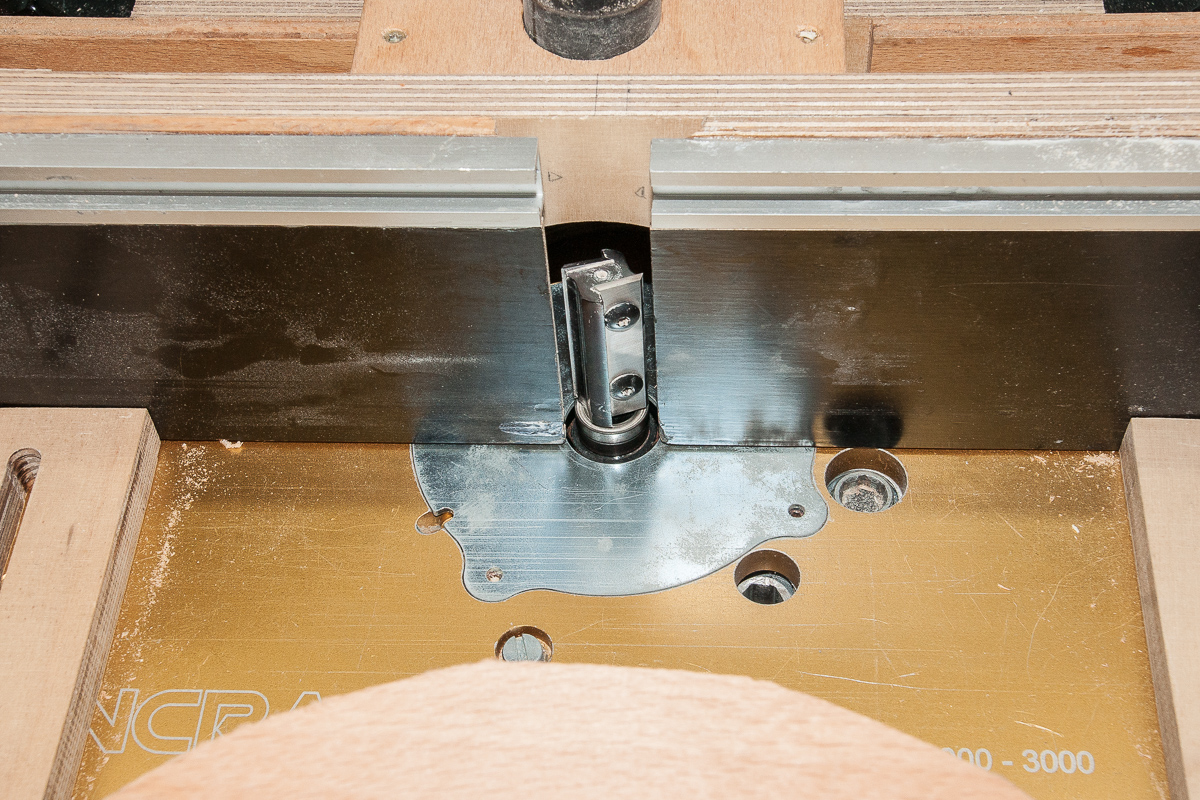
In dieser Konstellation kann die Höhe der schon sauber kreisförmig bearbeiteten Abschnitts auf ca. 55 mm vergrössert werden.
Das Werkstück ist fast genauso hoch wie der Fräsanschlag. Zwar könnte man die verstellbaren Backen gegen eine Variante mit 200 mm Höhe austauschen und dann auch wieder den Fräserschutz montieren, aber das ist letztendlich nicht notwendig.
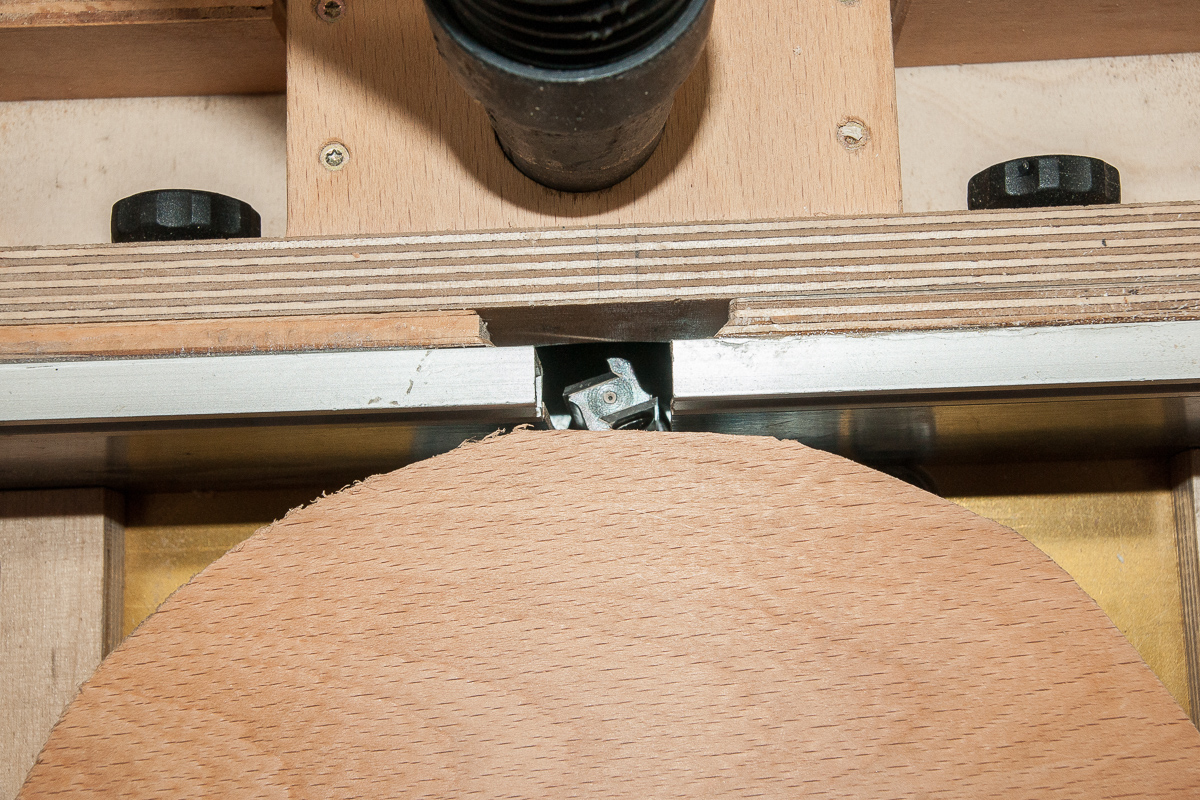
Danach geht es wieder mit dem anderen Bündigfräser - Kugellager unten - weiter. Auch das Werkstück wird gewendet. Der schon bearbeitete Abschnitt liegt nun erneut oben.
Genau wie beim kleineren Werkstück wird nun der Rest bearbeitet. Die Spanabnahme beträgt wie beim ersten Fall kaum 1,5 mm.
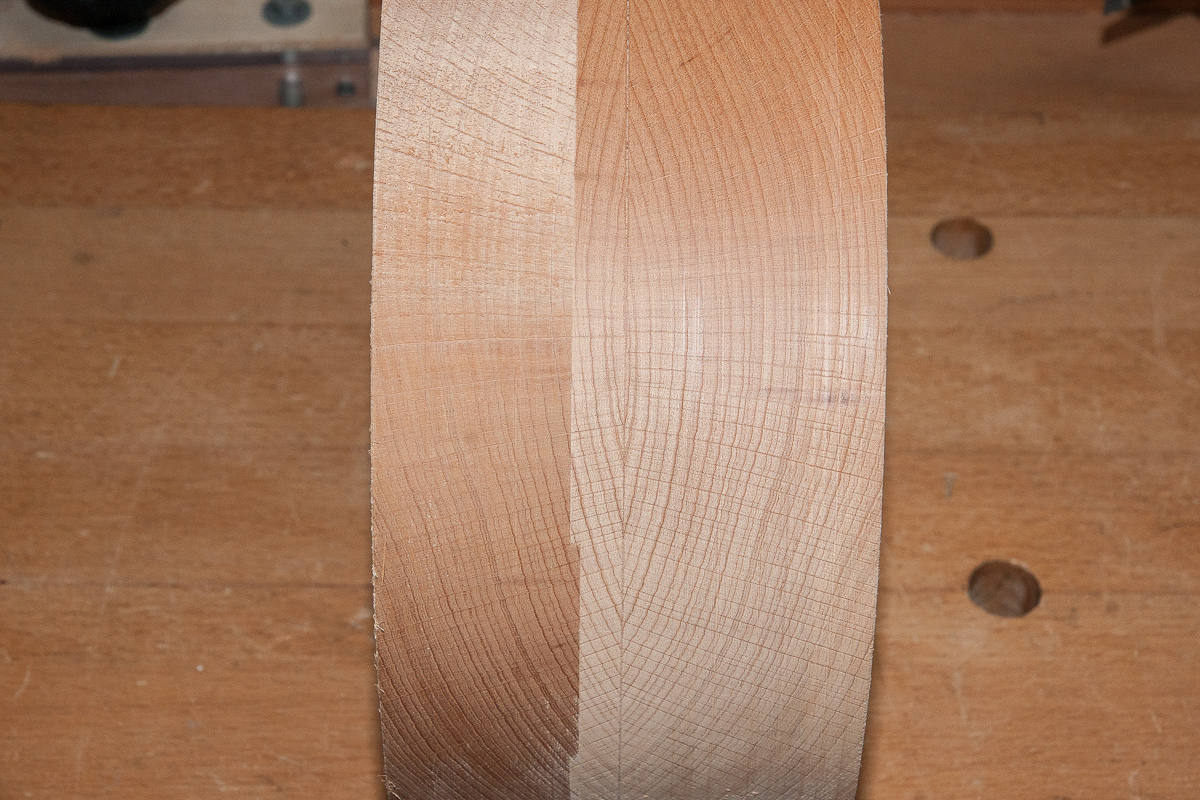
Welche Materialstärke wäre mit der beschriebenen Methode maximal bearbeitbar? Immer noch relativ konservativ gerechnet sind wohl um die 105 mm realistisch, eventuell auch noch geringfügig mehr.
Wird ein Kreisring gebraucht? Auch das gelingt relativ einfach wie die verlinkte Seite zeigt.