Stott Park Bobbin Mill
Juli 2014. Im Lake District (Cumbria) liegt im dichten Wald nahe des Lake Windermere die historisch Stott Park Bobbin Mill. Gegründet 1835 war die Fabrik bis 1971 in Betrieb. Sie fertigte wie mehr als 60 andere Mills im Umkreis auch Garnspulen für die grossen Spinnereien, die im England des 19. Jh. als eine frühe Grossindustrie entstanden.
Die Gegebenheiten begünstigten den Aufbau des Unternehmens. Es gab viel Wald, der den Rohstoff lieferte und durch die relative Steilheit des Geländes Zugriff auf Wasserkraft zum Antrieb der Maschinen. Dass die höheren Lagen der Gegend sehr niederschlagsreich sind war ein weiterer Vorteil. Um den Wasserfluss regulieren zu können legte man Kanäle, Dämme und Teiche an.
Als die Mill - bitte nicht mit "Mühle" übersetzen, Fabrik ist der passendere Ausdruck - in Betrieb ging bediente man sich eines Wasserrads von wahrscheinlich 24 ft. (ca. 7,3 Meter) Durchmesser. Transmissionen übertrugen die Drehbewegung auf die unterschiedlichen Vorrichtungen und Maschinen der Anlage.
1858 ersetzte man das Wasserrad durch eine Turbine, die einen besseren Wirkungsgrad besass. 1880 kam eine Dampfmaschine von 30 PS Leistung hinzu. Nun konnte man sich auf zwei voneinander unabhängige Kraftquellen stützen. Sich alleine auf die Dampfkraft zu verlassen wäre gewagt gewesen, da es in der Nähe keine Kohlevorkommen gibt und der Transport des Brennstoffs auf schlechten Strassen problematisch war.
Die Turbine lief - zweimal erneuert - bis 1941, wurde zu diesem Zeitpunkt durch einen Elektromotor ersetzt. Damit war das letzte Ausbaustadium erreicht, das bis zum Zeitpunkt der Schliessung des Unternehmens 1971 Bestand hatte. Das Aus kam durch die billigeren und leichteren Spulen aus Kunststoff.
Die Dampfmaschine ist auch heute noch vorhanden, man kann sie in Bewegung sehen . Ein neuer Kessel wurde 1991 installiert.
1983 nahm das Department of Environment - die Anlage war in Staatsbesitz übergegangen - den Betrieb der Fabrik als "Working Museum" auf und übertrug sie im Jahr darauf an English Heritage, einer staatlichen Institution, die sich um Pflege historischer Stätten kümmert.
Stott Park Bobbin Mill liegt 1,5 Meilen/2,5km nördlich von Newby Bridge neben der A590.
Die English Heritage - Website zur Mill: Stott Park Bobbin Mill
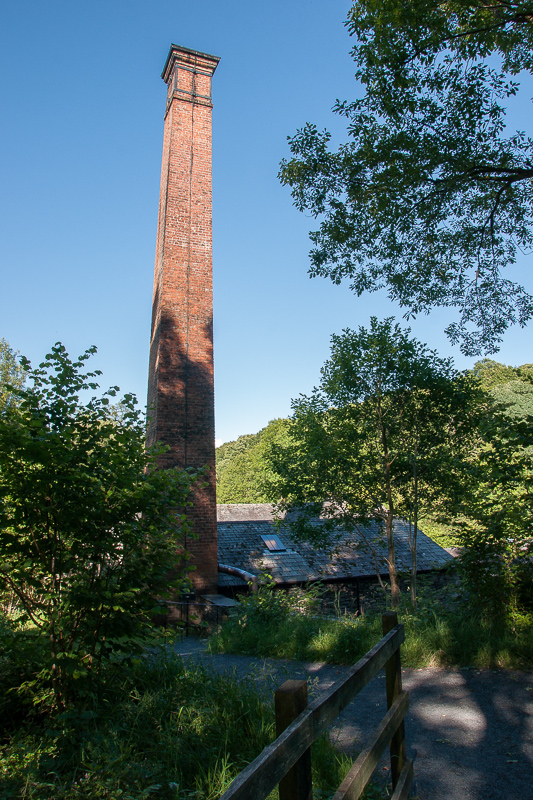
Materialbeschaffung
Obwohl die Täler und Hänge im Lake District stark bewaldet sind, war bei der grossen Anzahl holzverarbeitender Firmen doch eine besondere Art nachhaltiger Forstwirtschaft erforderlich.
Bäume wurde so gefällt, dass die Wurzelstöcke erneut austrieben. Nach ca. 15 Jahren waren die neuen Austriebe stark genug, um als Rohmaterial für die Spulen dienen zu können. Pro Hektar konnten bei einer Ernte ca. 25.000 dieser in etwa armdicken Stämme geschnitten werden. "Coppicing" nennt man diese Technik, "coppice" steht für Niederwald, Gebüsch, Unterholz. Verarbeitet hat man Esche, Erle, Birke und Weide, eventuell auch noch andere Arten. Das geerntete Holz wurde in offenen, überdachten Schuppen vorgetrocknet, bevor es verarbeitet werden konnte.
Jer nachdem ob es sich beim Rohmaterial um dicke Stämme oder die nachwachsenden, wesentlich dünneren Triebe handelte, waren unterschiedliche Verarbeitungsschritte gefragt. Dicke Stämme wurden zu Holzscheiben aufgeschnitten, deren Stärke um einen bestimmten Betrag grösser als die Länge der anzufertigenden Garnrollen war. Das dünne Holz wurde zuerst auf ca. 2-3 Fuss (60-90 cm) Länge gekürzt um danach in mehr oder minder zylindrische Stücke passender Länge geschnitten zu werden.
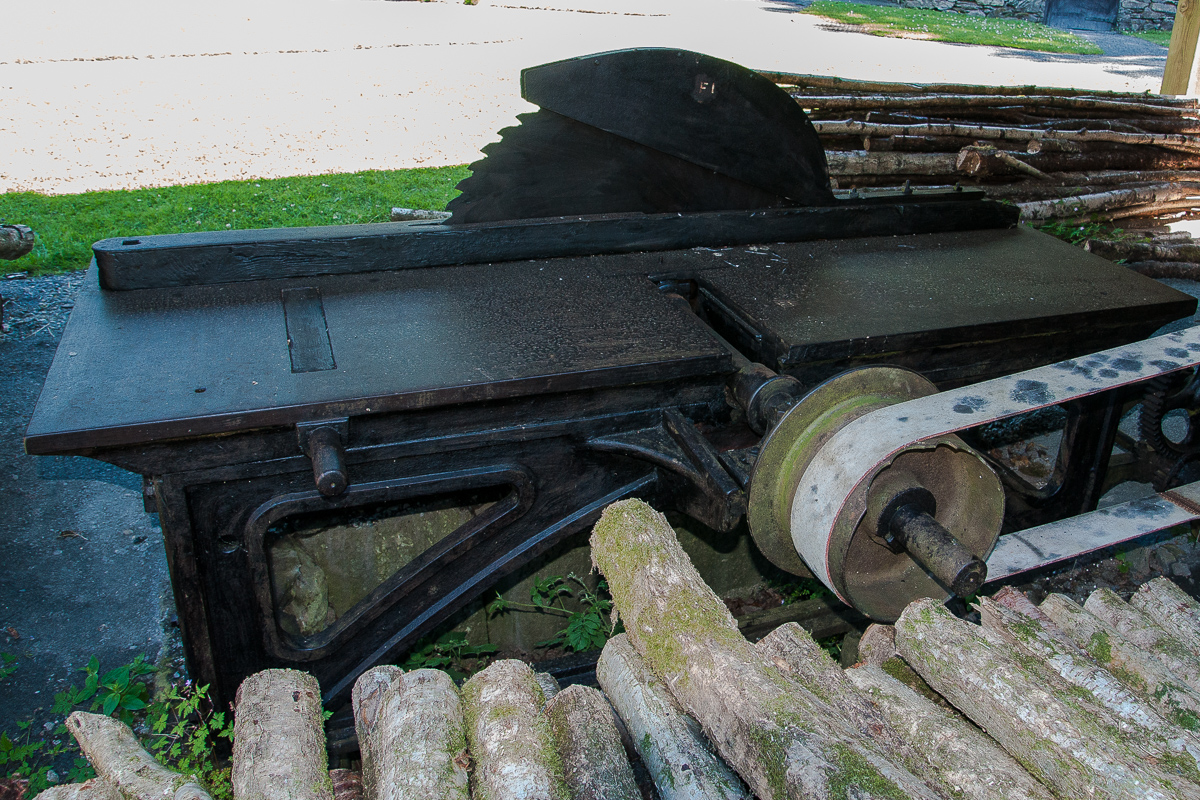
Die Kreissäge wurde mittels Riemen von der Transmissionswelle, die durch die Mauer des Gebäudes nach Aussen verlängert war, angetrieben. Im Hintergrund sieht man die geernteten Neuaustriebe, im Vordergrund einen Stapel der schon dimensionierten Stämme.
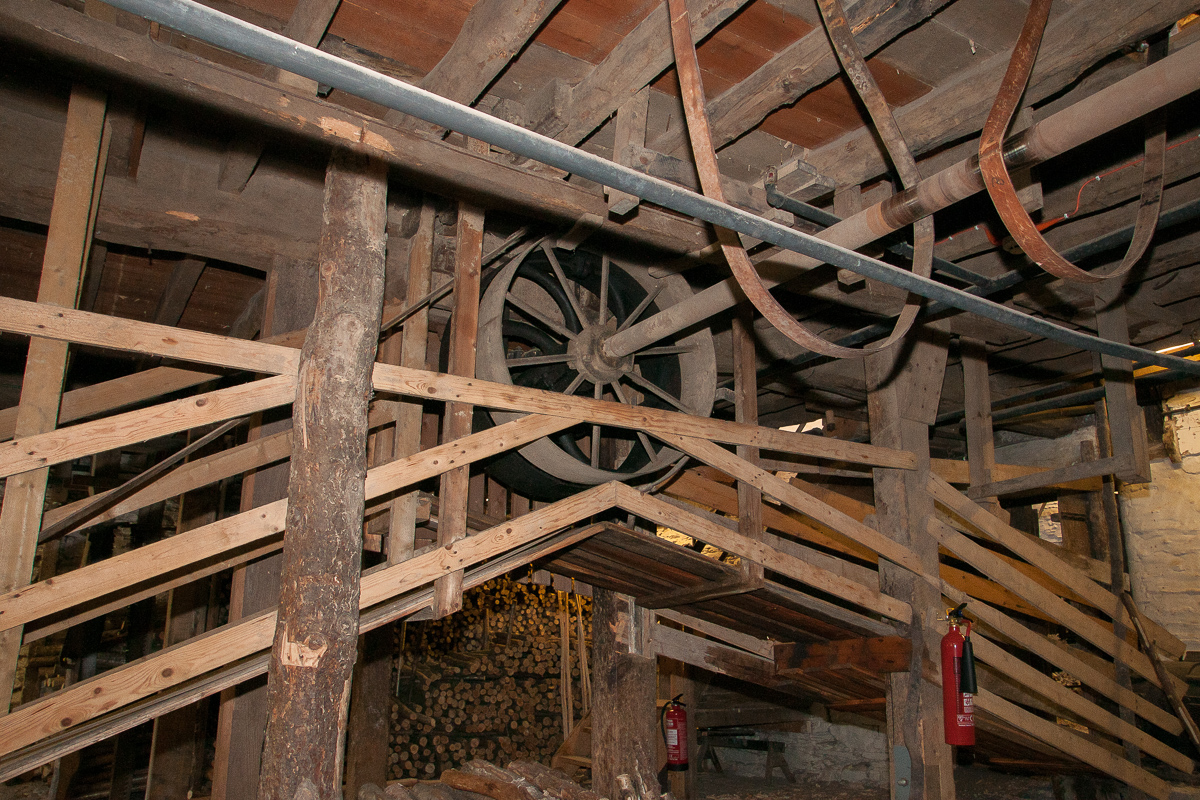
Im Hintergrund erkennt man Stapel mit den auf handhabbare Länge geschnittenen dünnen Baumstämmen
(Wie man sich denken kann gehören die Feuerlöscher nicht zur historischen Ausstattung.)
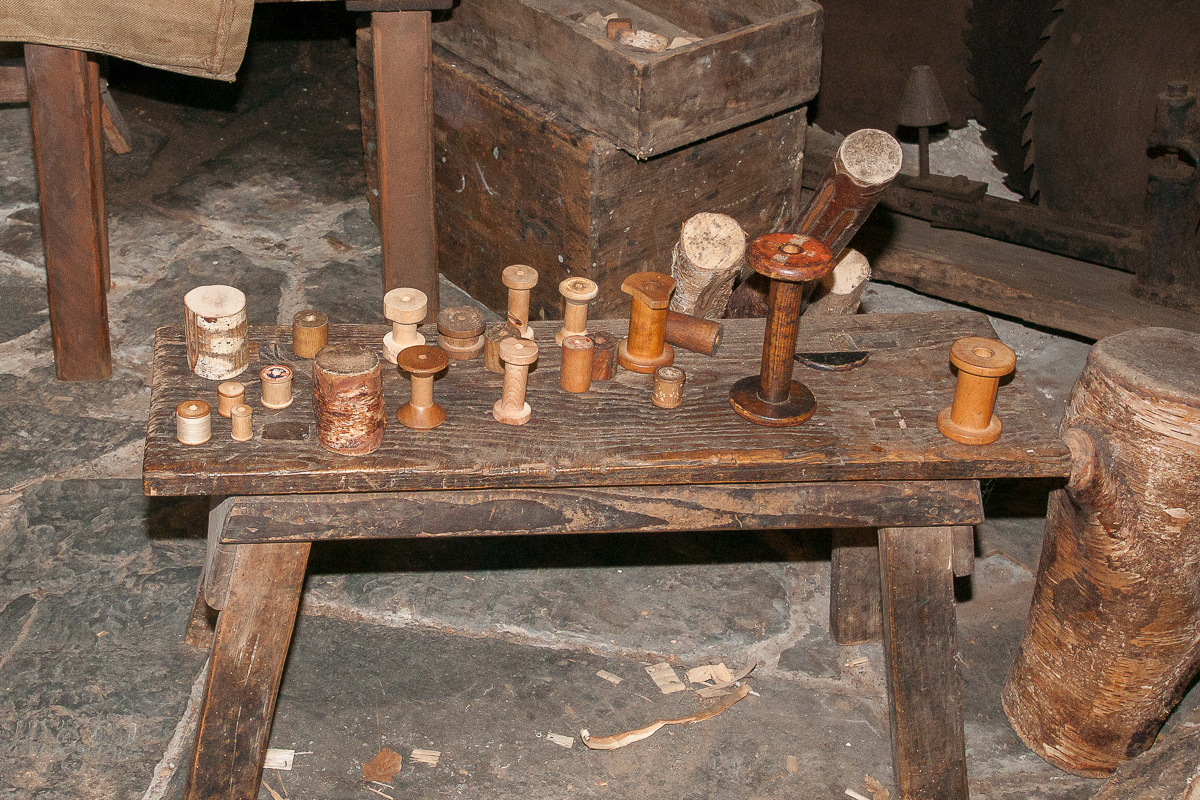
Herstellungsverfahren
Die meisten Spulen wurden aus einem Stück Holz gedreht, die grosse Spule weiter rechts ist älter, sie wurde dreiteilig gefertigt. Zwei Scheiben und der schlanke Wickelkörper sind miteinander verleimt.
Im Hintergrund wieder Muster der dünnen Stämme, auf der Bank zusätzlich noch weitgehend unbearbeitete Rohlinge.
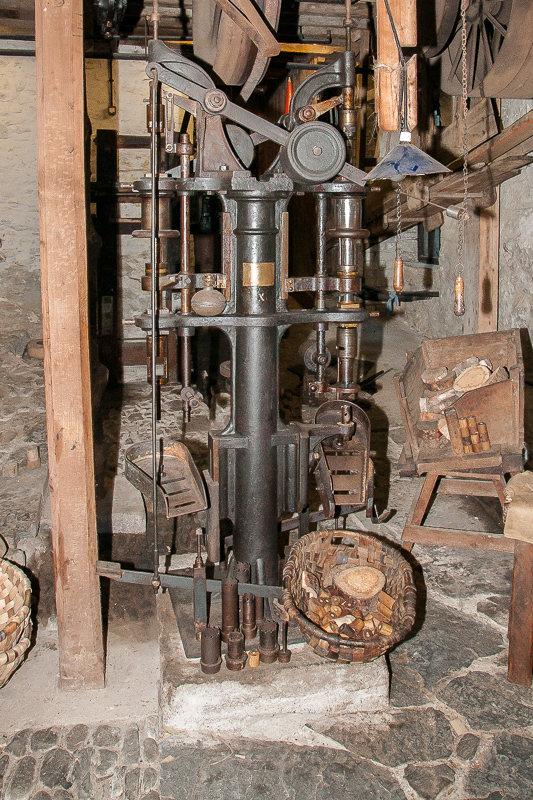
Diese Maschine diente zum Aussägen zylindrischer Rohlinge aus grossen Baumscheiben, die an der Kreissäge auf brauchbare Stärke geschnitten worden waren.
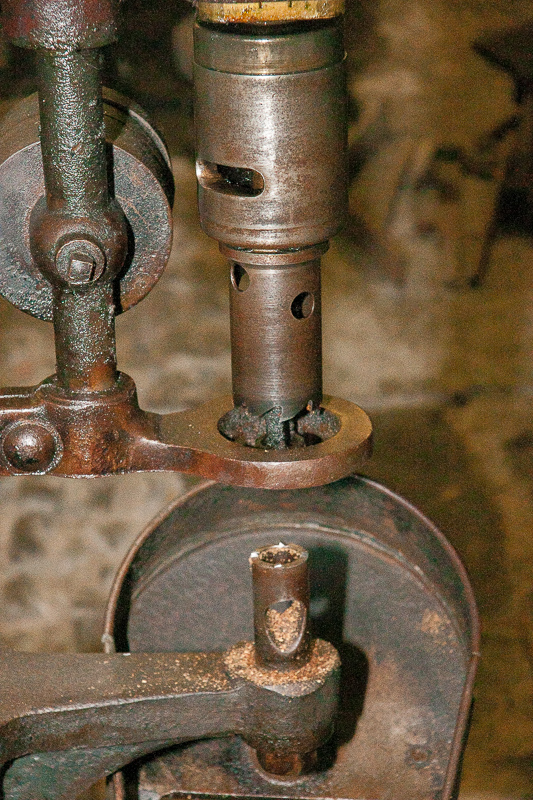
Je nach gewünschten Durchmesser konnten unterschiedliche Bohrer eingesetzt werden. Wieviele Rohlinge aus einer Baumscheibe gewonnen werden konnten, hing natürlich von der Baumscheibe, aber auch vom Geschick des Bedieners ab.
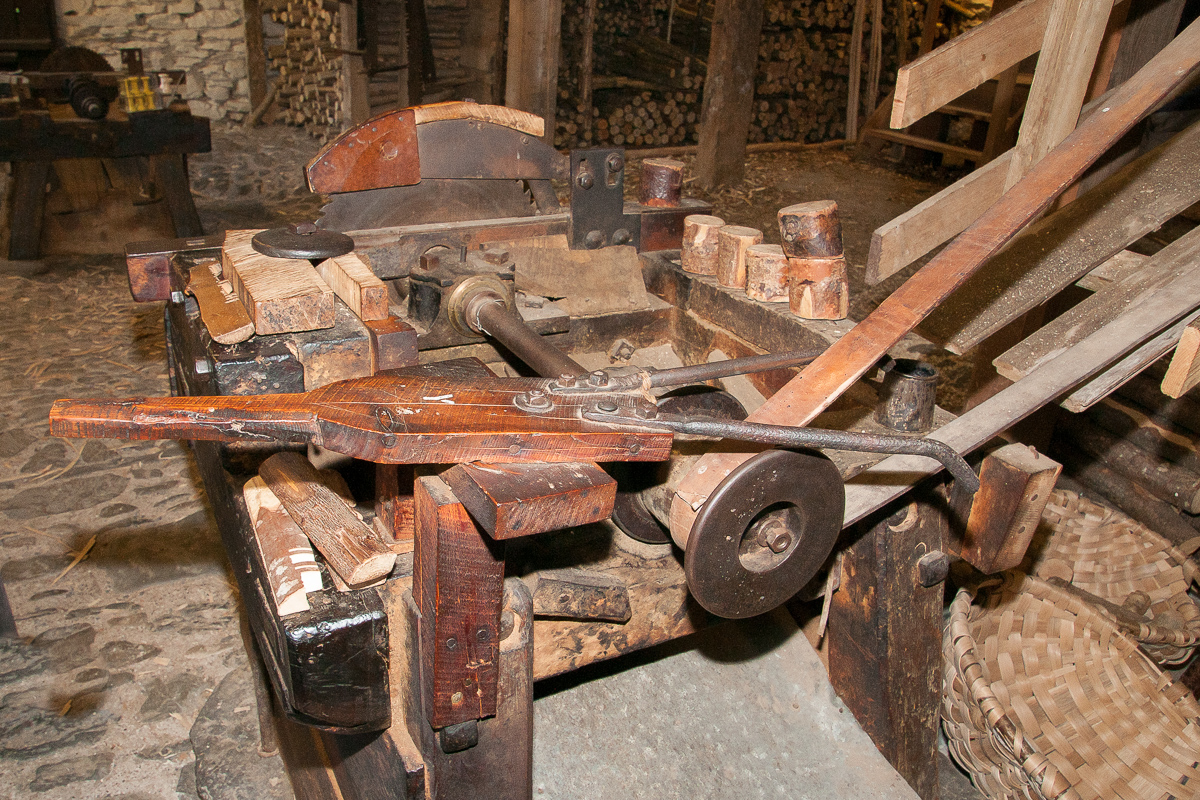
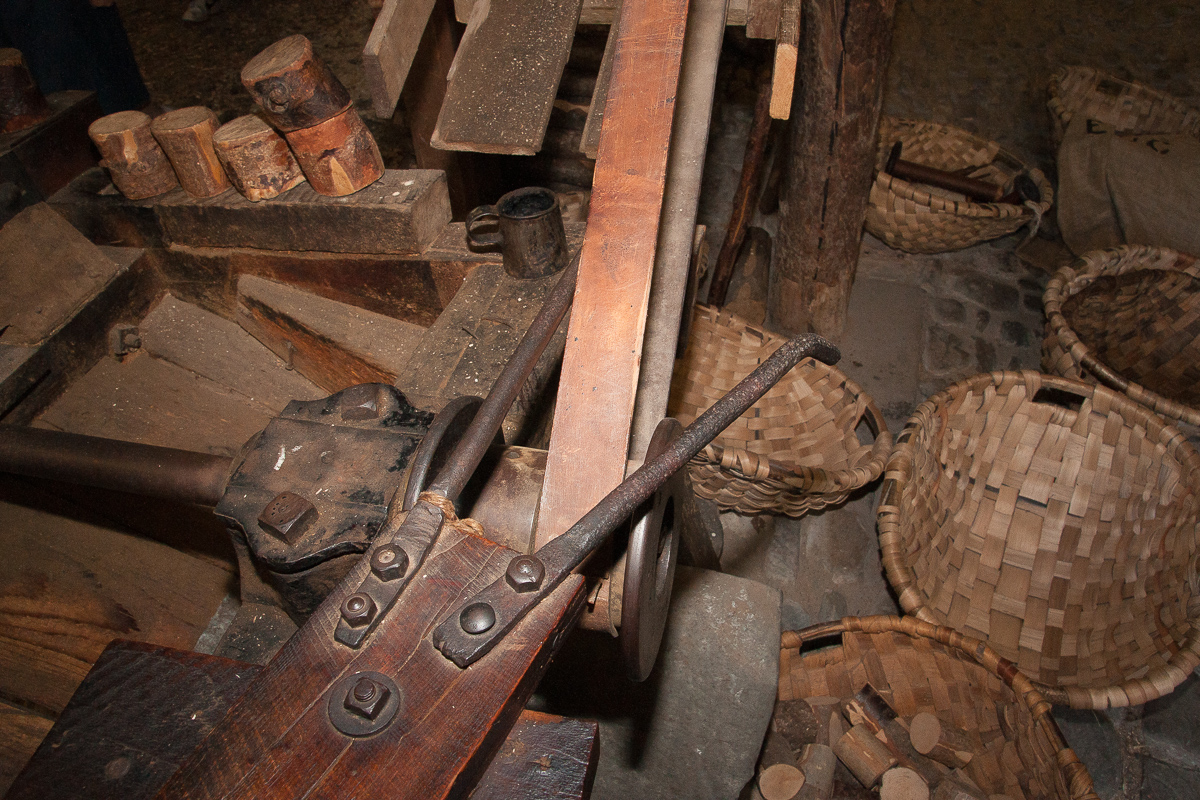
Je nachdem, welcher Spulentyp hergestellt werden musste, schnitt man auf dieser Maschine entsprechende Holzlängen ab.
Die Maschine wird direkt von der Transmission angetrieben. Einstellarbeiten bzw. Blattwechsel waren nicht ganz trivial, weil Antrieb während des Betriebs nie stillstand. Man löste das Problem so: Auf der Antriebswelle des Sägeblatts läuft eine zweite Riemenscheibe, die nicht fest mit der Welle gekoppelt ist, also frei dreht. Mit Hilfe der im Vordergrund sichtbaren Gabel konnte der Treibriemen von einer Scheibe auf die andere verschoben werden, die Säge so zum Stehen gebracht werden. Theoretisch! Denn durch die unvermeidbare Restrebung der frei drehenden Scheibe rotierte das Sägeblatt durchaus weiter, wenn auch mit wenig Kraft, bis es z.B. mittels eines Holzes blockiert wurde.
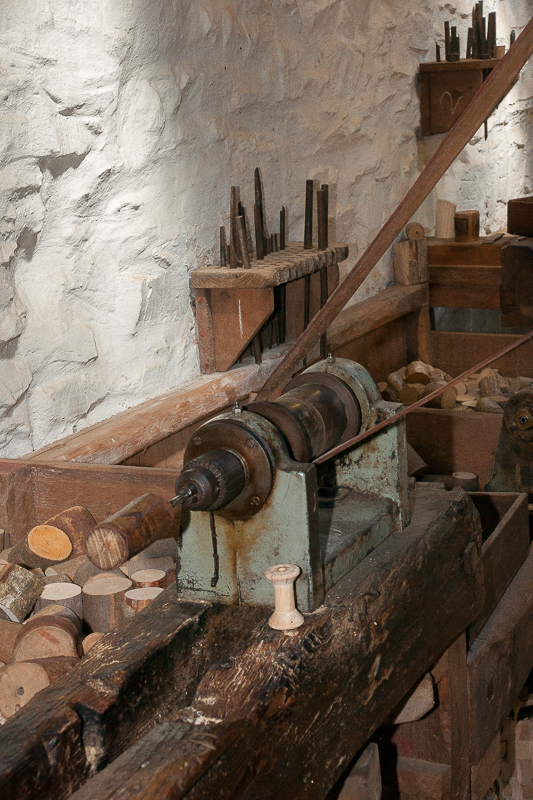
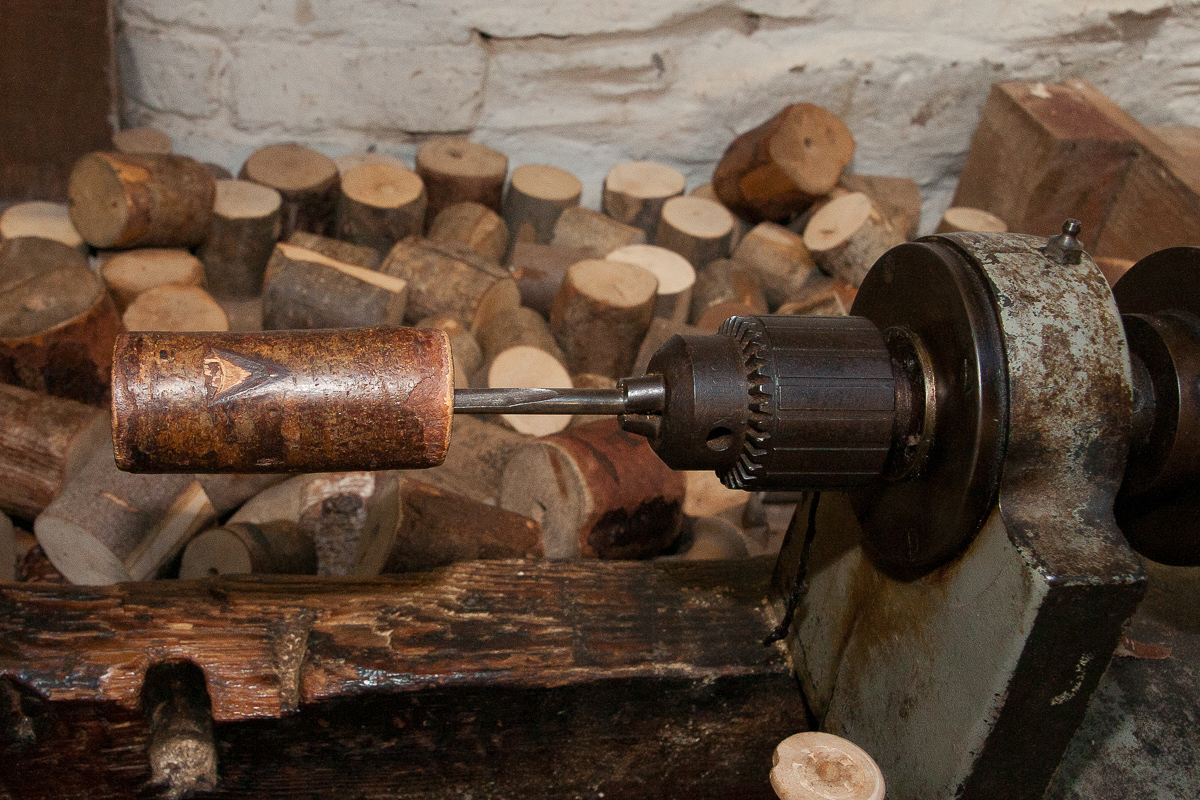
Die Maschine zum Bohren der Kernlöcher war nicht ohne! Auch sie konnte nicht einfach ausgeschaltet werden, drehte stets weiter. Das zu bearbeitende Werkstück wurde vom Arbeiter mit der Hand gehalten und nach Augenmass waagerecht und zentral durchbohrt. Zur besseren Spanabfuhr zug der Bearbeiter das Werkstück zwei- oder dreimal vom Bohrer herunter, danach ging es tiefer.
Problematisch wurde die Sache dann, wenn das Material auf dem Bohrer frass. Dann rotierte das Holzstück mit, gefährdete die Hände desjenigen, der an der Maschine arbeitet.
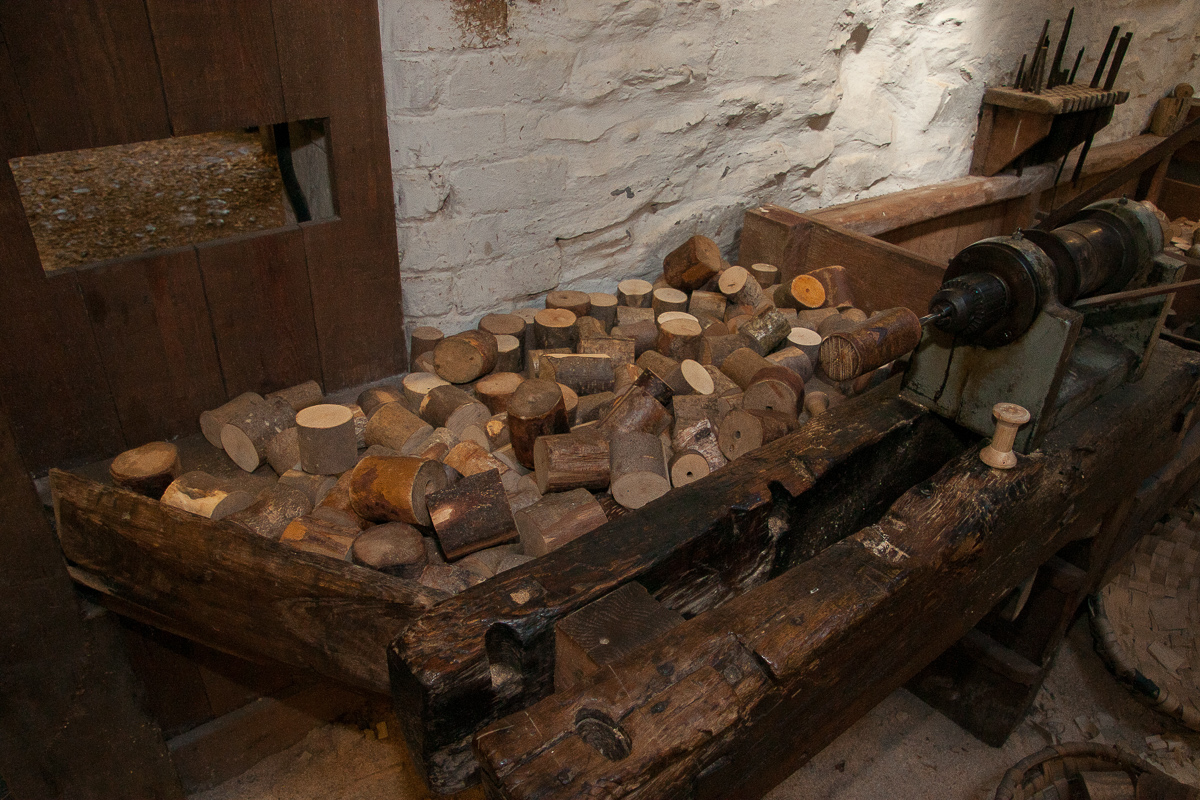
Überall in der Mill stellt man fest, dass die Unfallgefahr allgegenwärtig war. Arbeitsschutz im heutigen Sinn war weitgehend unbekannt. Das blieb offenbar auch bis zum Einstellen des Betriebs in 1971 so, ein Zustand, den man sich heute kaum noch vorzustellen mag.
Kinderarbeit kam hinzu. Erst ab 1867 durften keine Kinder unter 8 Jahren, ab 1878 keine unter 10 mehr beschäftigt werden. 10 - 14-jährige arbeiteten noch bis zur folgenden Jahrhundertwende in den Betrieben.
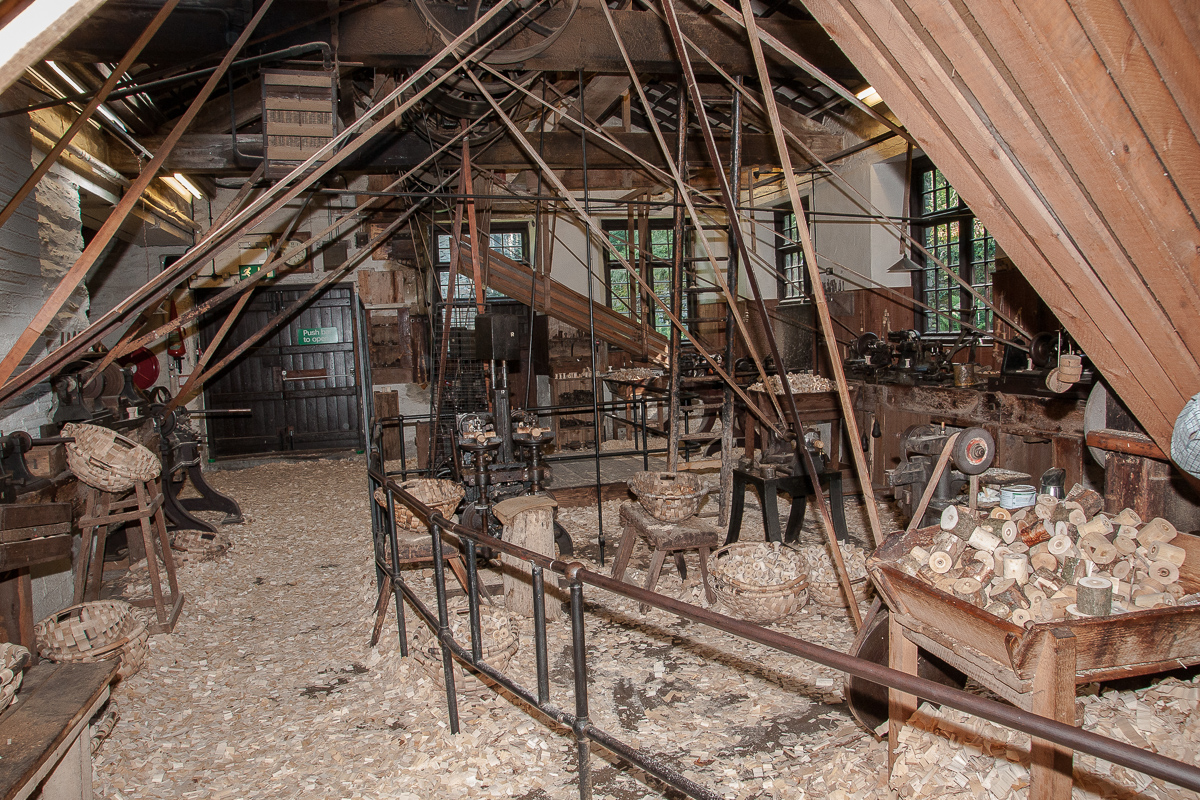
Unweigerlich produzierte man bei der Fertigung der Spulenkörper grosse Mengen Späne. Diese lagen besonders im Winter oft mehr als kniehoh, dienten als wärmende Isolation. Heizung gab es nämlich im ganzen Werksbetrieb nicht. Selbst im recht milden England nicht angenehm.
Bei all den Arbeitsumständen ist es schon verwunderlich, dass die Fabrik nie abbrannte. Brennstoff hätte es wahrlich genug gegeben.
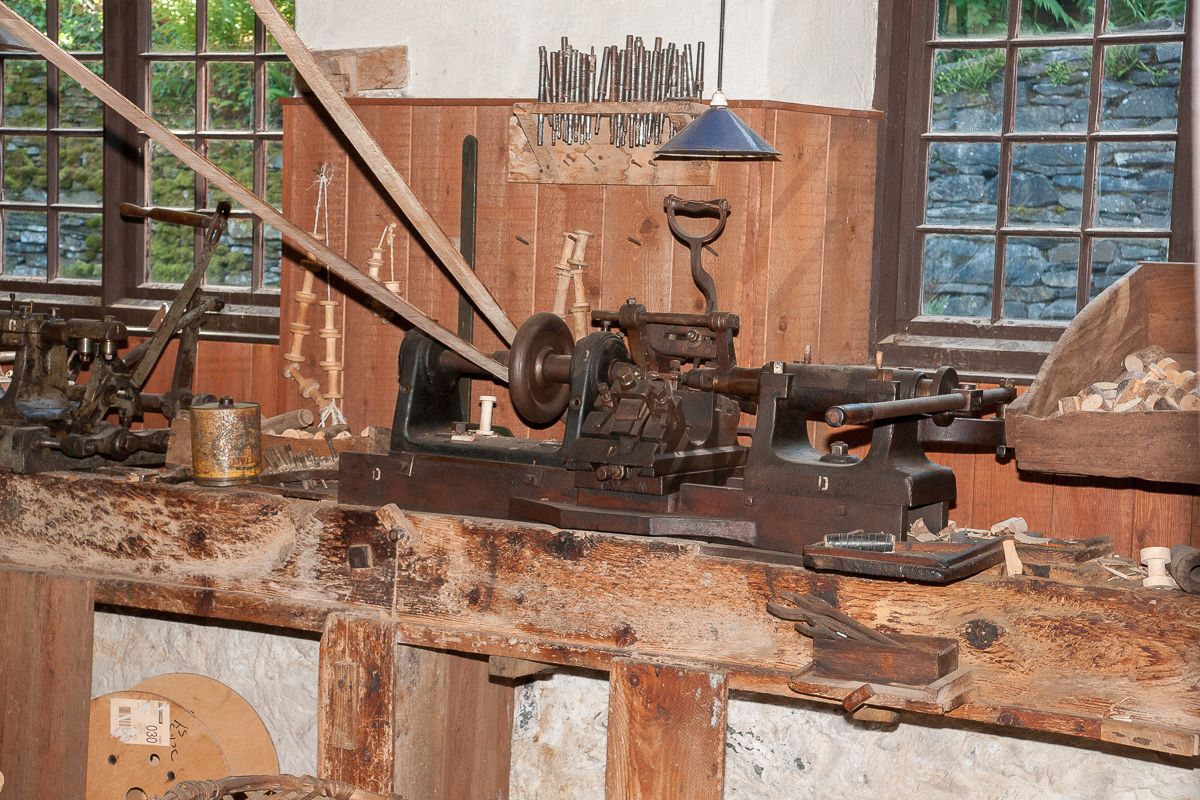
Diese Maschine gab den aus einem Stück gefertigten Spulen ihre Grundform. Eine Spitze griff in die zuvor gebohrte Zentralbohrung ein. Mit dem Hebel rechts wurde das Holz gegen eine mit Zacken versehene Antriebsscheibe gepresst und so in Drehung versetzt.
Mit dem Handgriff oben konnte ein breites Messer gegen das Holzstück gefahren und dieses damit auf den gewollten Aussendurchmesser geschnitten werden, Bewegte man den Handgriff in der Gegenrichtung, kam ein zweites, schmäleres Messer zum Einsatz, dass das Innere der Spule bis auf den Kern ausdrehte.
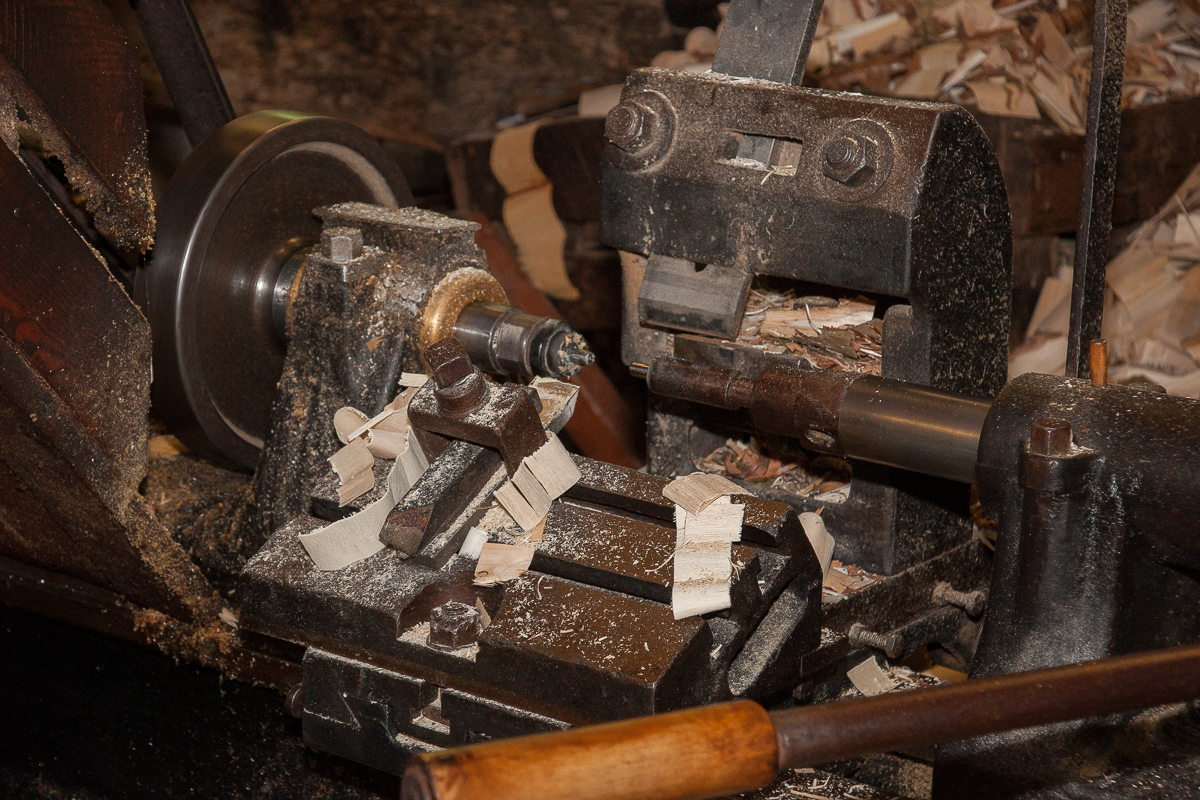
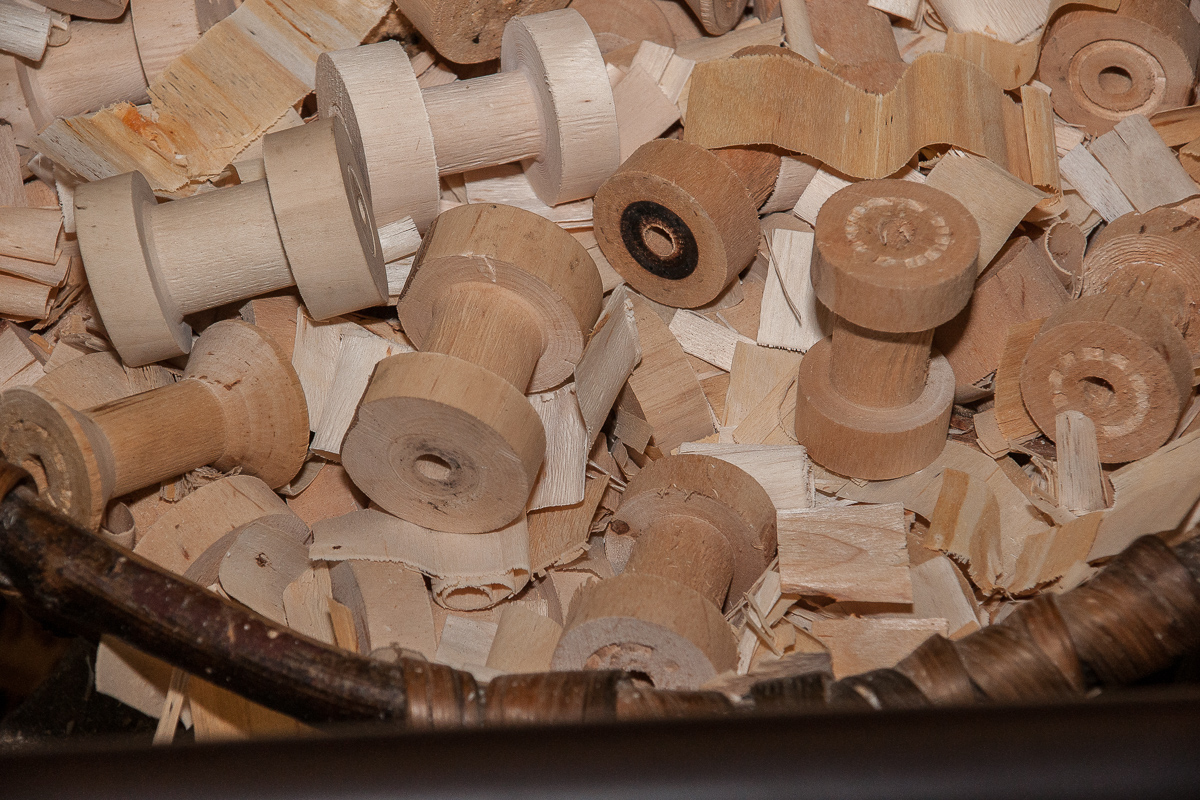
An den abgedrehten Rohlingen sieht man die typischen Abdrücke, die die Mitnehmerzähne der Antriebsscheibe hinterlassen.
In der vorliegenden Form waren die Spulenkörper noch nicht fertig. Die inneren Wangen der Seitenscheiben mussten noch abgeschrägt werden. Wie das dann aussah kann man an der einen Spule unten links erkennen.
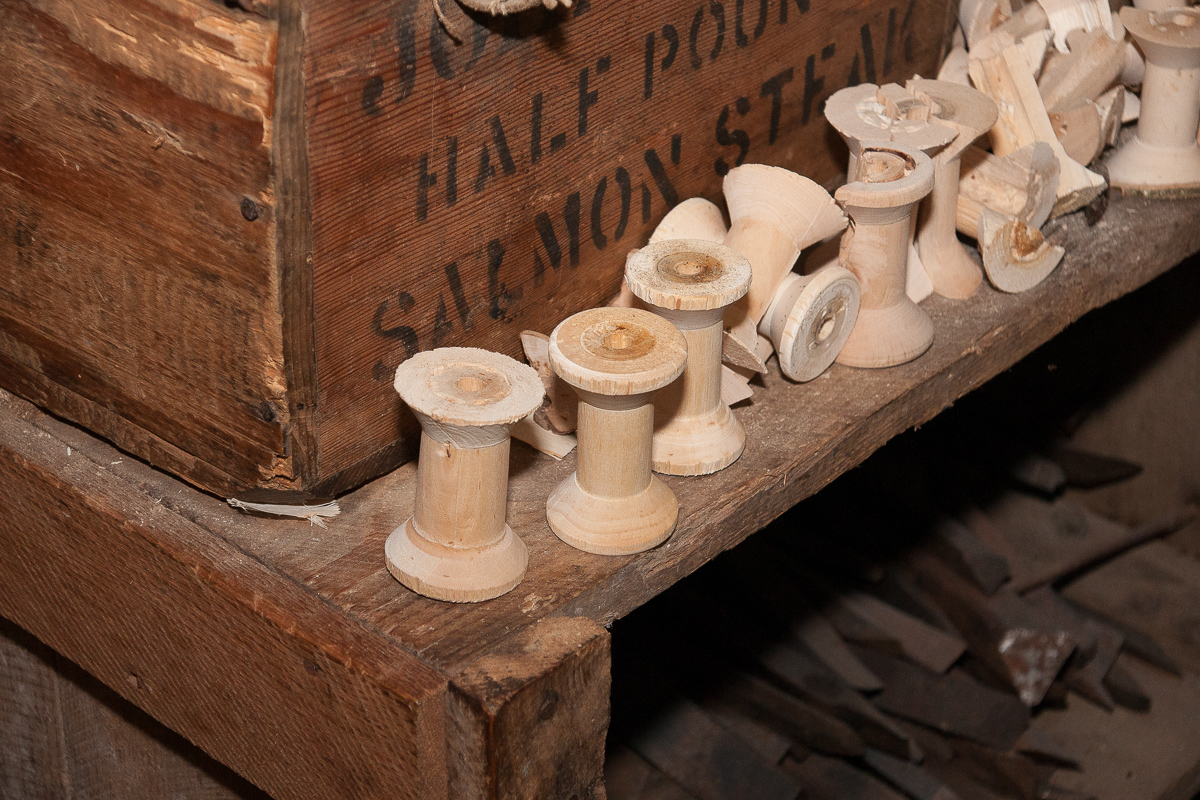
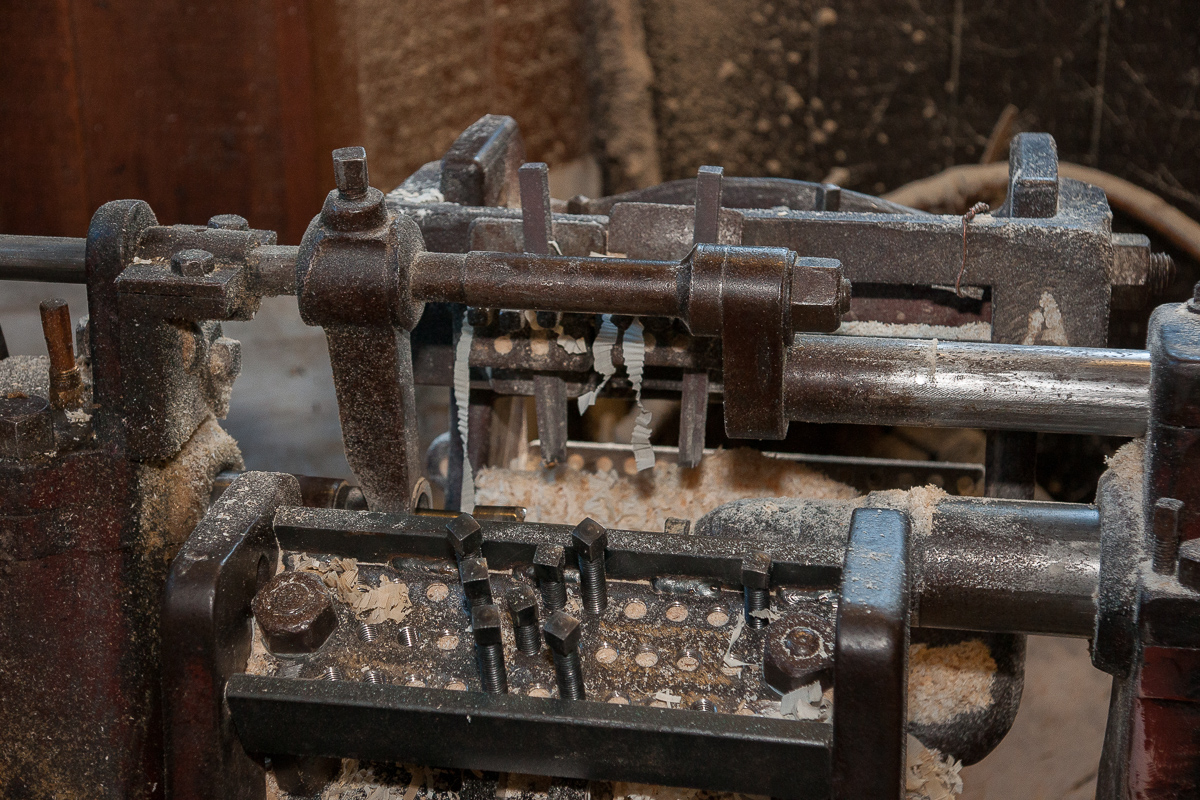
Die Fertigung blieb natürlich nicht über die gesamte Dauer des Bestehens der Fabrik auf demselben Stand, aber viele Einrichtungen waren so einfach und für den jeweiligen Arbeitsschritt ausreichend, dass es wenige grundlegende. Modifikationen gab.

Eine davon war diese Maschine, eine halbautomatische Bohrvorrichtung, um die Zentalbohrungen in den Spulenrohlingen herstellen zu können. Vier Werkstücke können auf einem Drehteller platziert werden. Ein von oben auf das Holz drückender Arm verhindert das Rotieren des Rohlings, der durch die V-Kerbe gleichzeitig richtig positioniert wurde. Damit konnte der Fertigungsdurchsatz gesteigert werden.
Im Obergeschoss der Fabrik wurden die Produkte schliesslich zuende bearbeitet bzw veredelt. Auf grossen Rosten trennte man verbliebene Späne von den gefertigten Artikeln.
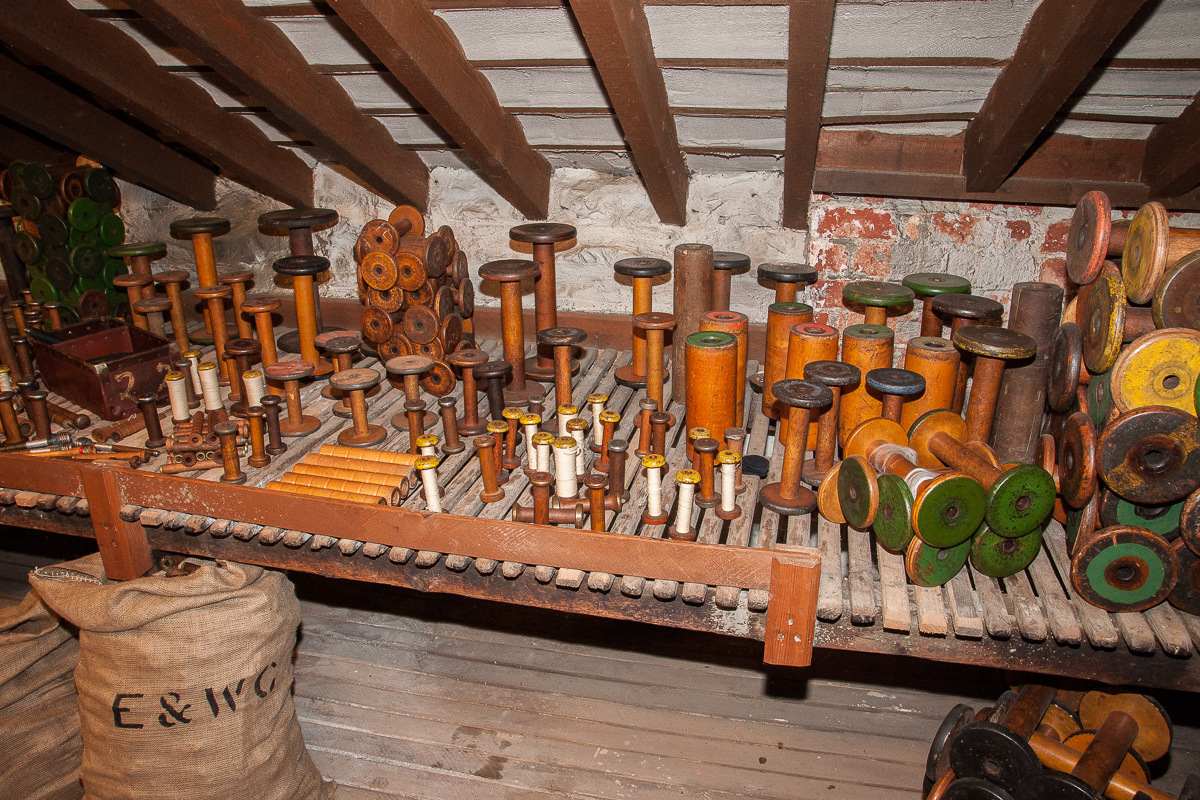
Heute findet man auf einem der Gestelle eine Auswahl der unterschiedlichsten Produkte, die während der aktiven Zeit hergestellt wurden. Nicht nur Spulen, sondern auch Tritte für Strickleitern, Knöpfe und Werkzeuggriffe entstanden - eben alles was sich an kleinen Teilen aus Holz drehen liess.
Einige Fertigungschritte wie das Zusammenleimen der dreiteiligen Spulen können anhand der Ausstellung nicht recht nachvollzogen werden, was dem Ganzen aber keinen Abbruch tut.
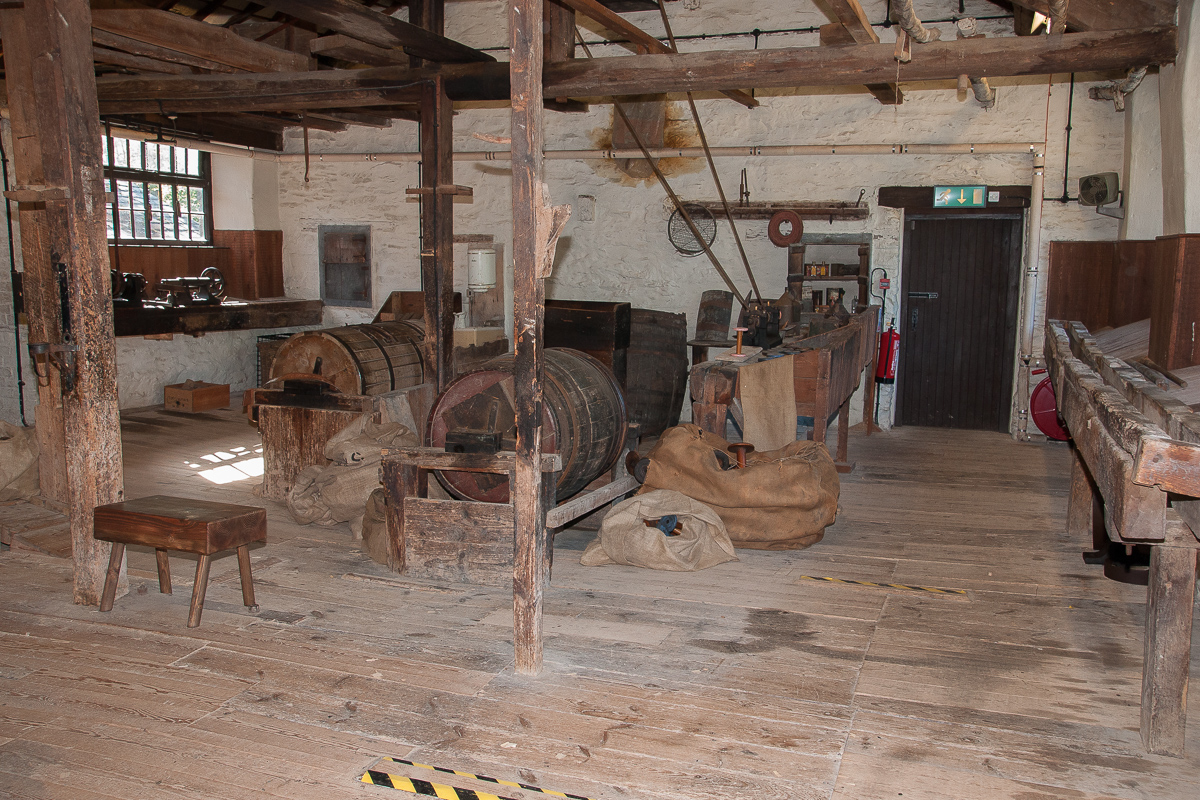
Die Fässer wurden mit Spulenkörpern und Paraffin gefüllt und in Drehung versetzt. Die Prozedur führte zu einer polierten Holzoberfläche. Pro Woche sollen angeblich rund 250.000 Spulen die Fabrik verlassen haben.
Grössere Spulen erhielten einen Überzug. Die Lacke, deren Lösungsmittel auf Alkoholbasis verdampften und gelegentlich bei den Arbeitern zu rauschartigen Zuständen führten (?), sollen angeblich den Begriff "Happy Hour" geprägt haben. Das kann man aber getrost als Urban Legend abtun, schon 1599 benutzte Shakespeare im Stück "Henry V" den Begriff.
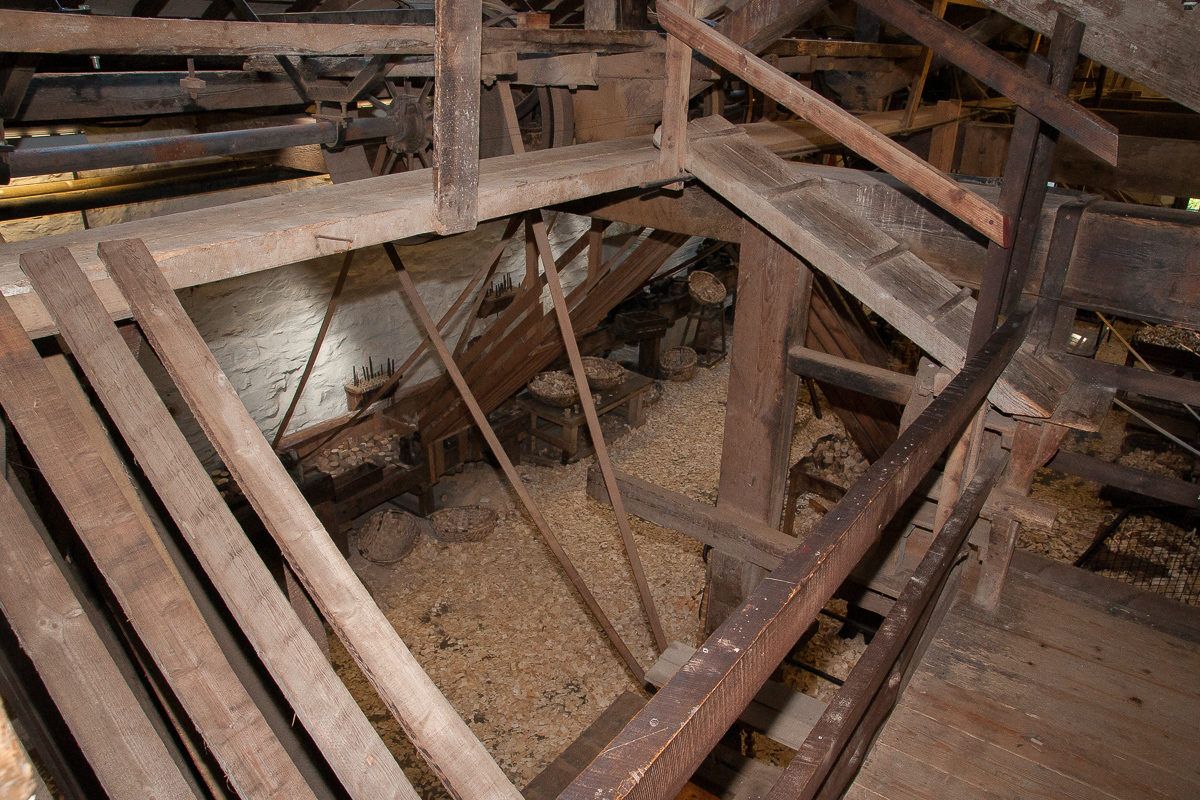
Arbeitsbedingungen
Gefertigt wurde in einer Art Akkord. Die Besonderheit bestand darin, dass für eine Mindestmenge Produkte kein Lohn gezahlt wurde, erst die darüber hinaus gehende Menge wurde entlohnt. Lange Arbeitsstage garantiert!
Kinderarbeit war anfangs an der Tagesordnung. Da es im Umkreis der Fabrik nicht ausreichend Bevölkerung gab, wurden Kinder (Jungen) aus Erziehungsheimen in Lancashire quasi als Zwangsarbeiter beschäftigt. In den 1860er Jahren kam es zu ersten staatlichen Inspektionen, die von ausgesprochen gefährlichen Arbeitsbedingungen berichteten. Danach setzten peu a peu staatliche Regulierungen ein.
Wer in jungen Jahren im Betrieb anfing, musste eine siebenjährige "Lehrzeit" durchlaufen. Erst danach wurde er zum regulären Mitarbeiter.
Zwischen 1861 und 1865 kam es zu ernsthaften Schwierigkeiten durch einerseits Überkapazitäten der Spinnereien und andererseits den amerikanischen Bürgerkrieg, der den Import hochwertiger Baumwolle aus den Südstaaten der USA nahezu vollständig unterband. Diese hatten zuvor rund 80% des Rohmaterials geliefert.
Die Preise für Baumwolle stiegen rasant auf ein Mehrfaches, viele Spinnereien entliessen ihr Personal. Damit wurden natürlich auch keine Garnspulen mehr gebraucht. Auch hier wurden die Arbeiter entlassen. In kurzer Zeit wurden viele Menschen auf ein Niveau zurückgeworfen, in dem ein Überleben kaum noch möglich war. Staatliche Programme linderten die schlimmste Not, caritative Organisationen halfen mit. Gewinner waren oft die Baumwollhändler, die Bestände bunkerten und zu Phantasiepreisen absetzen konnten. Die Vorkommnisse sind unter der Bezeichnung "Lancashire Cotton Famine" in die Geschichte eingegangen.
Dampf
Wie schon weiter oben erwähnt unterlag die Versorgung der Fabrik mit Energie verschiedenen Entwicklungsstufen. Die Zeit der Dampfmaschine ist beim Rundgang am leichtesten nachzuvollziehen, obwohl die Transmission heute bei den Vorführungen von der letzten Ausbaustufe, einem Drehstrommotor, angetrieben wird. Das ist einfacher und kostengünstiger.
In früheren Zeiten heizte man den Dampfkessel auch mit den Abfällen des Betriebs. Naheliegend, wenn man bedenkt, welche Mengen Holzspäne anfielen. Für volle Maschinenleistung dürfte diese Feuerung aber nicht ausreichend gewesen sein.
Dampf war besonders im Sommer wichtig. Das Tageslicht war lange verfügbar, entsprechend lange wurde gearbeitet. Gleichzeitig gab es nur ein reduziertes Angebot an Wasserkraft. Also musste die Maschine nachhelfen.
An Wochenenden kann die Maschine in Bewegung bewundert werden. Wann, das muss man erfragen? (Zitat: "During certain days of the month, visitors can see the old steam engine being fired up.")
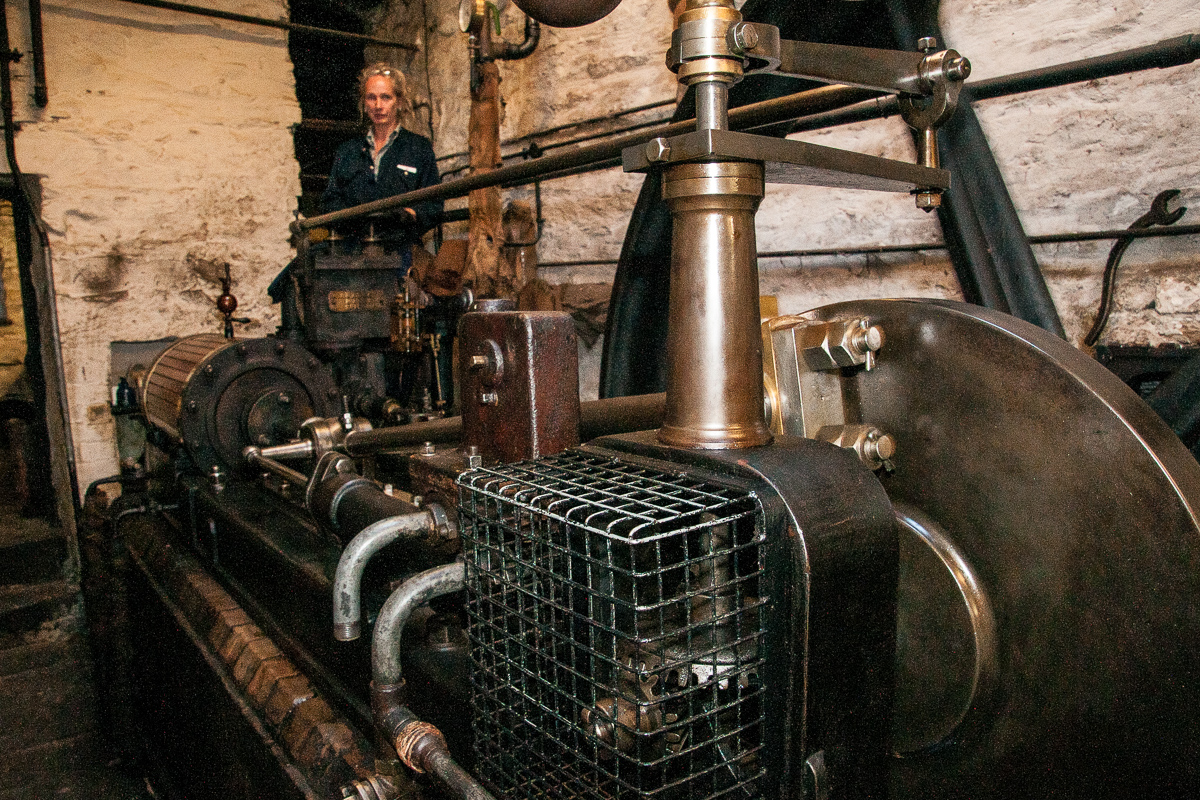
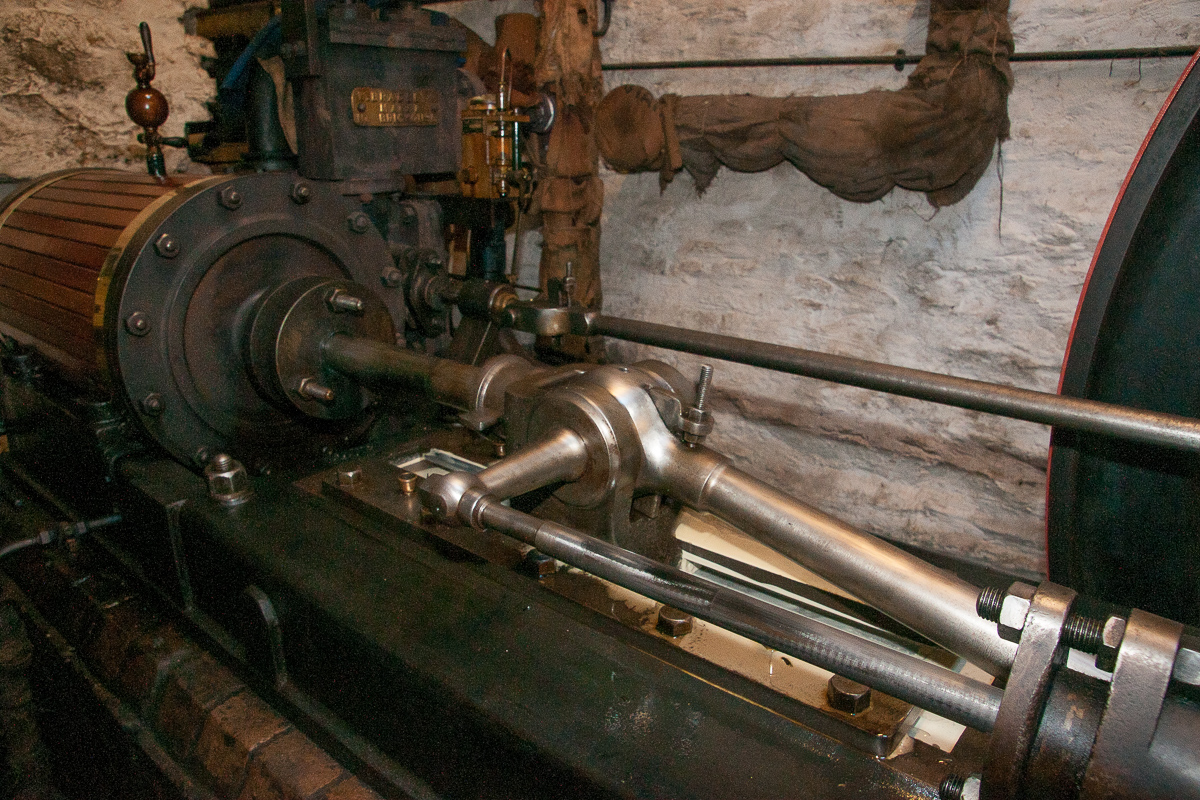
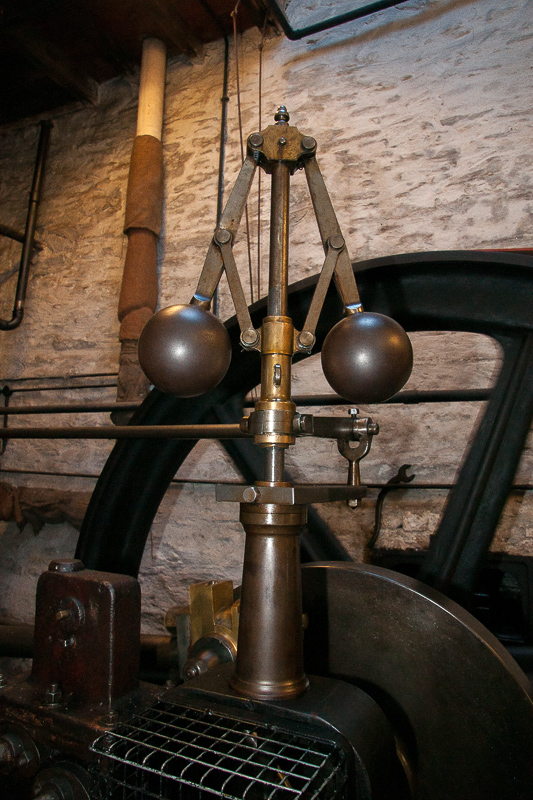
Es handelt sich um eine liegende, einzylindrige Maschine mit Dampfexpansion und Kreuzkopf. Sie leistet 30 PS, wurde 1880 von W. Bradley, Gooder Lane Iron Works in Brighouse (West Yorkshire) hergestellt.
Eisen
Werkzeuge aus Eisen wurden in einer Schmiede in einem Nachbargebäude angefertigt, die Eisen in einer im Obergeschoss über der Spulenfertigung befindlichen Wertstatt scharf gehalten. Angeblich war jeder Arbeiter für den brauchbaren Zustand seines Werkzeugs selbst verantwortlich, also auch für das Schärfen. Wohl gehörten die Eisen oft auch den Arbeitern.
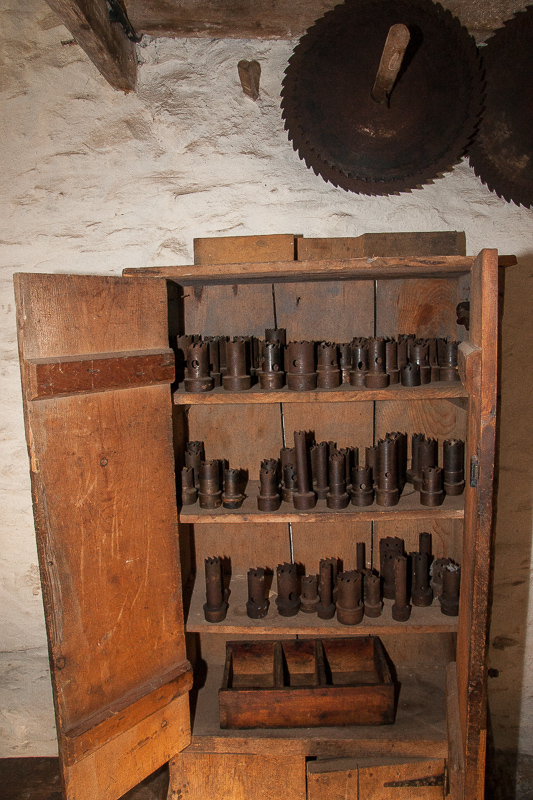
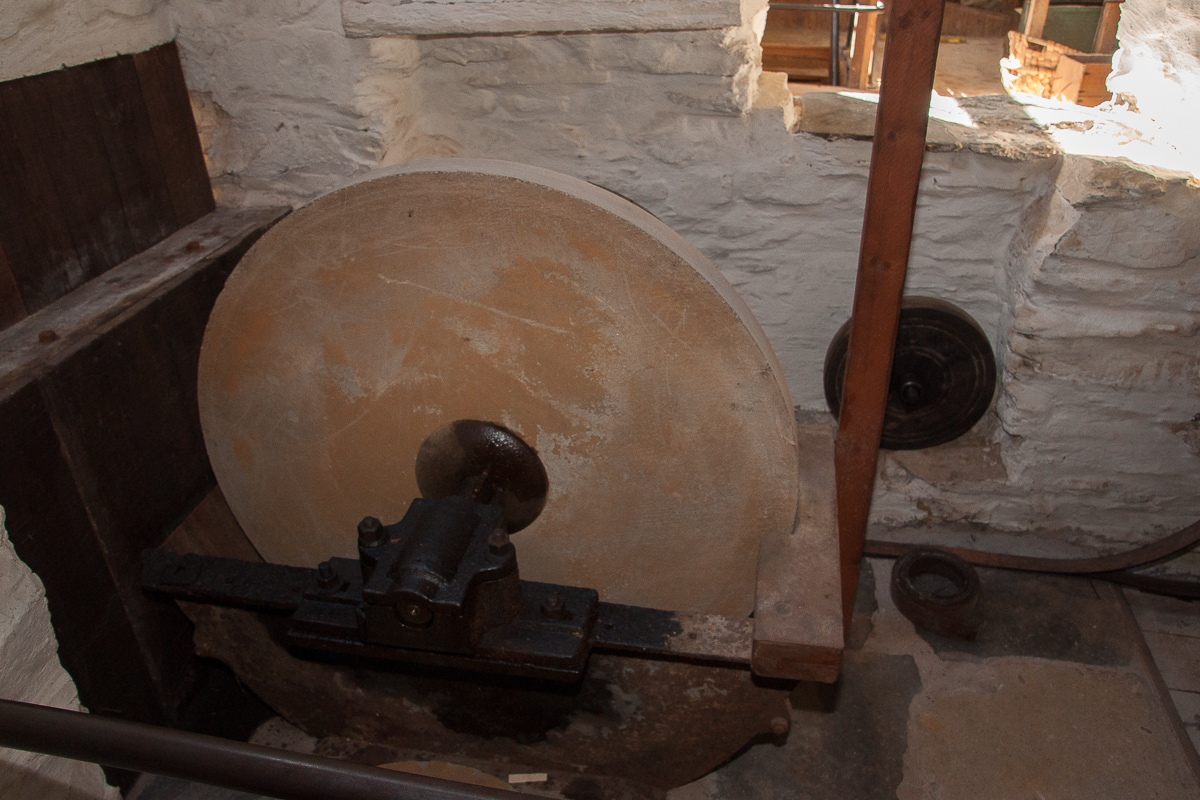
Besucher können im Freigelände die künstlich angelegten Dämme und Teiche finden. Sozusagen ums Eck liegen die Reihenhäuser, in denen zumindestens ein Teil der Belegschaft wohnte. Auch die alte Schmiede mit den Trockeräumen für Spulen im Obergeschoss - auch über dem Dampfkessel gab es derartige Trockenanlagen - existiert noch. 4 acres Wald gehören zum Gelände, laden zum Wandern bzw. Picknick ein.
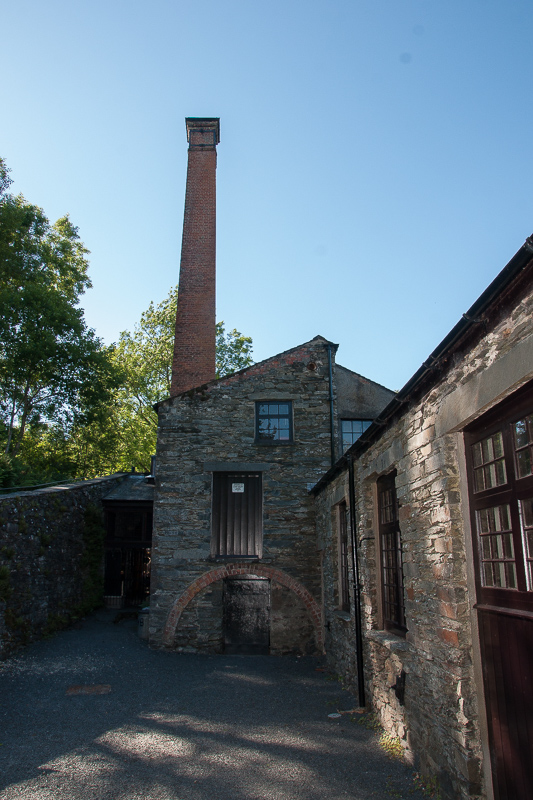